Roof Flashing Repair
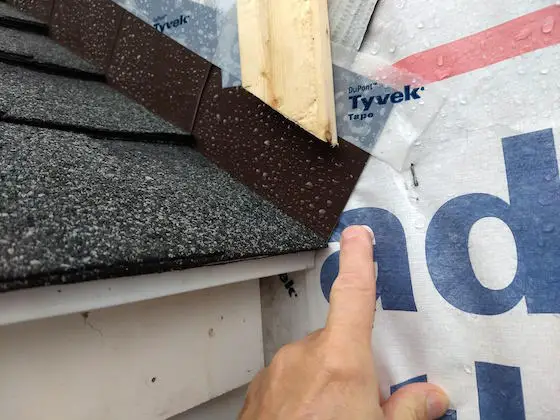
The brown bent aluminum is step flashing. The aluminum extends under the shingle and goes up the roof under the next flashing about 2 to 3 inches. The roofer made a SERIOUS ERROR where my finger is pointing. There should be an additional piece of flashing that's called a kick-out flashing. The lower end is bent and soldered and directs the water out to the front face of the exterior siding or stucco. Copyright 2018 Tim Carter
"Flashings are things that stop leaks around things that pop up through your roof."
Roof Flashing Repair - Most Roof Leaks are at Flashings
The sources of a wide majority of residential roof leaks are roof flashings. For the most part, the correct installation of flashing material is what determines whether or not your roof will leak. The reason for this is quite simple.
What's the Best Way to Repair Roof Flashings?
I feel the best way to attempt roof flashing repair is to acquire full knowledge of what they are, what the best materials are, and how they're part of the entire roof system.
The last thing you should do is grab a can of black goo roofing cement or a few tubes of caulk thinking that's the way to repair a flashing. That's treating the symptom, not CURING the disease.
The vast majority of roofing products are quite easy to install. The manufacturers have engineered these products to be practically leak proof when they're installed on a simple roof.
However, there are very few simple roofs.
What is a Simple Roof?
A simple roof is one that doesn't have anything popping up through it. Examples of simple roofs are:
- dog houses
- small outdoor sheds
- firewood storage rack
Rarely will you find a plumbing vent stack, chimney, fan vent, pot vent, valley, a side wall projecting above the roof, etc. on a dog house.
You will, on the contrary, almost always find one of these items projecting through a residential house roof. The most common thing is a plumbing vent pipe. Watch this video to see how to make it leakproof for decades:
How Old is Roof Flashing Technology?
The engineering concerning flashings has been known for hundreds and hundreds of years. It is, in fact, very simple engineering. The system depends almost entirely on gravity. Gravity works with the flashing material and sheds the water onto the regular roofing materials.
If you use a flashing material that depends on some other method to shed water you can quite possibly develop a leak. Caulks, roofing cement, pitch, and similar materials depend on their stickiness or adhesive qualities to seal out water. These qualities can easily break down under constant exposure to the elements. If you want a leak-proof roof, stay away from these type of compounds.
Free & Fast Bids
What Are Flashings?
Flashings are things that stop leaks around things that pop up through your roof. Here's a list of common things that pop up through a roof:
- chimneys
- plumbing vent pipes
- dormers
- bath vent fans
- roof vents
How Long Should Flashings Last?
Roof flashings should last longer than the original roofing material.
Many people expect roofs to perform for a minimum of 15 to 20 years. Some roofs can be expected to last 50 to 80 years. This means that the materials which are used for flashings must have the same, or greater, lifespan as the roofing material itself.
What are the Best Flashing Materials?
The best flashing materials must also be able to be shaped easily and have the capability to be easily soldered, brazed or welded. This second point is crucial.
Copper, tin coated steel, lead, and galvanized steel are examples of fantastic traditional flashing materials.
Why Do Flashings Have to be Soldered?
The reason the flashing materials must have the capability of being soldered or brazed is quite simple. The soldering or brazing process of metal is similar to welding. These processes take two separate pieces of metal and make it one.
There are many, many times in flashing work where one has to bend around corners or splice two pieces of metal together.
These instances create seams which must be soldered or brazed. As I mentioned earlier, the flashing material must have a projected lifespan equal to or greater than that of the roofing material. Soldering or brazing metals together passes this test.
Do Flashings Have to Expand and Contract?
Flashing systems must also pass another test. They must be able to handle the constant expansion and contraction between roofing products and those things which are not roofing products. This battle of expansion and contraction can take place on a daily or seasonal basis.
The sun can create extremely hot surface temperatures during daylight hours, causing roofing materials to expand. At night, the temperature drops and the materials contract.
Do Flashings Move Because of Lumber Shrinkage?
Seasonal changes can cause the framing lumber to shrink and swell depending upon humidity and wood moisture content.
This shrinking and swelling cause the roof sheathing and rafters to move. The flashing materials must be able to withstand this movement and continue to be leak-proof. Well-engineered and installed two-part metal flashing systems can handle this movement with no problem.
On new construction, the framing lumber can shrink dramatically in the first year after construction. If one-part flashing systems are used, leaks can easily develop from the gaps that develop from the shrinking lumber.
Two-part flashing systems consist of a base or step flashing which is usually in contact or laced into the primary roofing material, and these are then covered by a counter flashing. The counter flashing is a separate piece of metal or building material which laps over the base or step flashing.
Should Counter Flashing Be Attached to the Flashings it Covers?
Counter flashing should not be attached (mechanically or soldered) to the base or step flashing. The two materials must be able to move independently of one another. The counter flashing can be made of a wide variety of materials. It can be wood siding, stucco, vinyl or aluminum siding, or other material which forms the outside surface of a wall.
In chimneys and along brick walls, the counter flashing is almost always the same metal which is used for the base or step flashing.
Does UV Light Hurt Metal Flashings?
Two-part metal flashing systems are not harmed in any way by the sun's ultra-violet (UV) rays. UV rays can easily defeat caulking, plastic roof cement or most other flashing substitutes. UV radiation can remove the elasticity of these products and make them brittle.
When they become brittle, they can no longer handle the daily expansion and contraction. Also, very few of these products have a lifespan equal to or greater than roofing products. They are temporary remedies at best. Only consider using them for emergency type repairs.
Should You Paint Roof Flashings?
Flashing materials that can rust (tin coated steel or galvanized steel) should always be painted. They often are not painted correctly by roofers. These metals must have special primers applied first and then the proper number of finish coats of paint.
Also, it's extremely important to wash these metals with soap and water or paint thinner before painting!!! These metals have a very light coating of oil which is applied during the milling process. If the oil is not removed, the paint job will fail. You will be battling peeling paint long into the future.
Is Aluminum a Good Flashing Material?
Aluminum is not a bad flashing material if you watch where you use it. Two big downsides to aluminum are:
- it can't be soldered with ease
- it corrodes if it touches brick or stone mortar
Avoid using aluminum flashing material. Aluminum cannot be soldered. Also, if it is used in flashing chimneys or brick walls, it will rapidly corrode. The chemical makeup of the mortar attacks and eats the aluminum! Do not allow your roofer to use aluminum!!!
Are Flashings the Most Complex Part of a Roof?
Yes, flashings are, for the most part, the most technical aspect of roofing. Their installation requires an experienced individual in almost all cases. Soldering vertical surfaces requires skill and knowledge. Professional roofers possess these talents. Professionals realize the importance of flashings. They know that flashings are the weak link in the chain. You should realize this also.
The art of installing flashings cannot be described in this short bulletin. In fact, many books do not fully cover the subject. You have to research several books to get the full picture. I have developed a partial list of some publications which do a good job of illustrating and explaining roof flashings.
Many of these are available at libraries or larger bookstores. I highly recommend that you consult several publications to get a full understanding of the complexity of roof flashings. The more you realize how complicated flashings are, the better your chances of hiring the best professional. Good luck!
Column B25
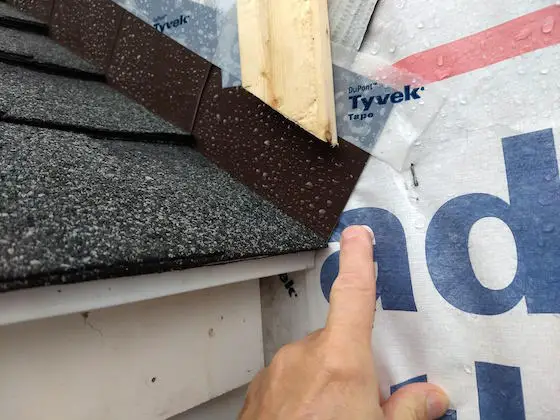
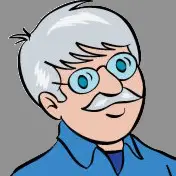
3 Responses to Roof Flashing Repair