Waterproofing Foundations
Foundation Sealer
You really can't be too careful when you start to build a new home. There are so many time-delay booby traps that can spring on you months or years after you move in. One that tends to shock many people is the simple task of waterproofing a foundation system. I can hear you now, "Tim, my builder did waterproof my foundation." Well, believe it or not in many cases that is not true.
What's the difference between damproofing and waterproofing?
Yes, your builder has already or plans to spray a black liquid on your foundation. He may even call it waterproofing. But the fact is this product may be just damproofing. There is a significant difference between damproofing and waterproofing. Because the buzzword mold is now as loud as the steel-against-steel clash of wheels on the rails of the L, you need to make sure the moisture from the soil can't possibly invade your new basement walls.
What causes that moldy smell in an old basement?
Perhaps the best way to start is to go back in time to a basement in an old home. Surely you can recall that smell, that dank moldy smell of an old basement. You were smelling mold and its growth was fueled by the constant stream of moisture from the soil through both the unprotected walls and through the concrete slab you walked across. Years ago, builders didn't regularly apply even a simple tar coating to foundations. They did not have access to large sheets of plastic that help retard the transfer of water vapor from soil through concrete slabs.
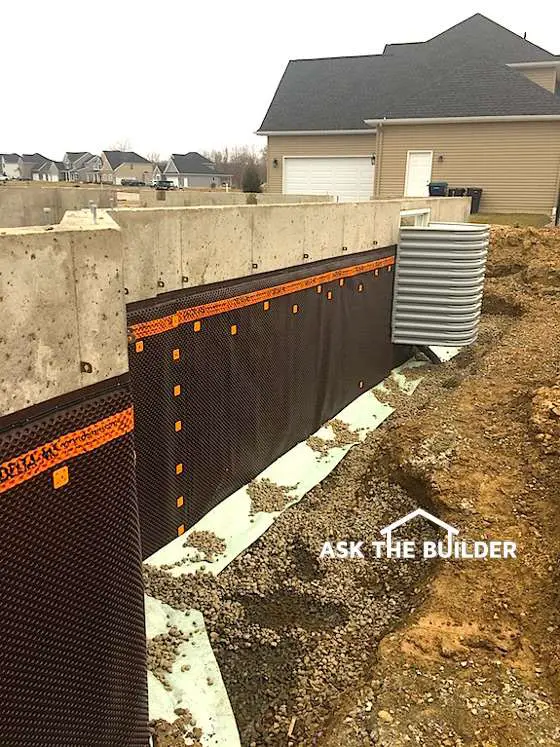
This system connects to the drain tile. It's a great waterproofing solution. I'd add more gravel and no matter what the MS Delta people say, I'd cover the gravel with a foot, or more, of straw. Copyright 2018 Tim Carter
And believe me, water vapor readily passes through concrete. Granted, it does not transfer at the same rate as perhaps paper or cloth, but it does move to an environment of lower vapor pressure. Liquid water can soak into concrete. Surely you have seen damp patches of concrete before. Proof of this is easy as efflorescence is a prime example of water movement. The water enters the concrete, dissolves salts and then moves towards your basement. Once at the surface of the concrete wall, the liquid water evaporates and leaves the salt deposits behind.
Prevent a wet basements by using this Basement Waterproofing Checklist to hire a great professional. I offer a 100% Money Back Guarantee.
To permanently stop water and water vapor from entering your foundation walls, you need to waterproof them. There are any number of systems that do this, but I prefer the spray-on systems that seal the pores of the concrete. But don't confuse waterproofing with damproofing, not for a moment.
Damproofing is an inexpensive way to meet the lowest minimum standard of the building code. The usual weapon of choice for damprooofing is simple hot liquid asphalt sprayed on the concrete. Liquid asphalt is an excellent damproofing material, but alone it is not a waterproofing system.
Do you need to check local building codes?
And while we are speaking of the code, here is one of the traps. Every local building code can be different, but most state that unfinished basement living spaces just have to be damproofed. But what happens if you know you are going to finish your basement a year or so after you move in? The answer is to waterproof the foundation now for that possibility and to ensure your basement will indeed stay dry even if it remains unfinished.
What is a good waterproofing method?
The waterproofing method I used on my own home is still available.
It was called Tuff-n-Dri at the time and it was pioneered by Owens-Corning. They subsequently sold off this business segment to Tremco.
It's a mixture of hot asphalt and rubber. The coating ends up being about one eighth inch thick or even thicker. A special insulating panel is placed in the hot liquid that helps protect the coating from damage during backfilling and it acts as both an insulator and a drainage plane. The rubber in the mixture imparts elasticity to the coating so if the foundation cracks, the coating stretches over the crack to provide protection.
If you’re interested in learning more about the cost of foundation waterproofing I have an article here.
Damproofing compounds can't do this. If the foundation wall cracks, and most develop tiny shrinkage cracks over time, water can readily pass through to your basement. It is also better to waterproof from the outside rather than try to stop water once it is already into your basement space. Spend the money now and waterproof before the builder backfills.
Over the years, I've seen many different spellings of efflorescence. Here's my growing list: effervesce, effervescence, effervescent, effleresants, effloreflance, efflorescence, efflorressance, effluorescence, eflorescence, eflorescents, ellforesce and ifflorescence.
Column NH058
23 Responses to Waterproofing Foundations