! ! ! See Author's Notes at Bottom of Column ! ! !
DEAR TIM: My husband and I are interested in buying a new home, but we found out that the lot the house was built on has two natural springs located on either side of the lot. The contractor had two French drains installed to divert the water from the springs as well as directing the down spouts from the roof into these drains.
We decided to investigate the crawl space. The walls of the foundation were dry, but my husband found several spots of water in the crawl space on top of the plastic sheeting. However, there was not water under the plastic sheeting where he found the water. The amount of water was around a tablespoon.
What, if any, problems might we experience if we decide to purchase this property? What suggestions do you have for us? We plan to go back to the property if and when a hard rain occurs.
Betty R.
DEAR BETTY: You might have all sorts of problems and then again you may have none. The first thing to determine is whether or not there are surface water issues in addition to the subsurface water problems you already know about. Read my past column about Lots - Important Features to get a handle on the overall grade of the lot.
The liquid water on the vapor retarder concerns me as I wonder how it got there. Was it just condensation that had formed under the retarder and then flowed out on to the membrane at a nearby seam? Or, did water somehow enter the crawlspace and run over the membrane and this small amount of water was the last to evaporate?
I would also ask exactly how the existing French drains were installed. It would be ideal if they were nearly identical to the method I have used for years. Read my past column about Linear French Drains to see a great 3D diagram of how they are constructed.
Author's Notes:
You may wonder if my advice is worth anything. Well, read what Jim Sanders wrote to me when he was at the end of his rope:
"Hi, I just wanted to write to give you the results of my "Trench Drain". I have had a wet crawlspace for 15 years. Water would fill the crawlspace at times, so we actually had to drill weep holes at the base so that it would enter the basement and eventually, the sump pump.
I have tried everything. Several contractors said that the only thing we could do was to bring the water into the house via drainage tile and let it enter the sump pump. That would work, but because I live on a 6' elevation, there is no reason that I should have water problems. It became like clockwork...when it rained, we would rush home from the lake or wherever we were vacationing so that we could be prepared to start the backup generator, in case the power failed. We even had our alarm company put a sump alarm on our system, so they could notify us if we had a power failure. Battery backup was not an option, because sometimes we lose power for days and during any rain, our sump would run every 7 minutes...just like clockwork.
I found your site and read the article on the trench or French drain. At first, it sounded a bit like "holistic healing" to me. I failed to understand why a 2 ft. deep trench, 4 ft. away from the house would do any good. How could this simple thing correct an extreme water problem that has plagued me for years, cracked my foundation, settled my garage floor and ruined almost every vacation?
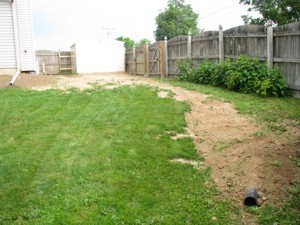
The Linear French Drain trench running from the house. PHOTO CREDIT: Jim Sanders
I decided "what the heck". I had to dig by hand using a trenching spade and a pick-ax, because the builder back-filled our property with brick and blacktop. It took quite a bit of time. Because the ground level varies so much on that side of the house, I was not able to achieve exactly 2 ft. deep. It varied from 18" to 30" in spots, but the slope was downhill. The trench is about 80 ft. long. At times, I thought about filling it all in, because I just didn’t believe that it would work.
I stoned it, put tile in, and filled it with #1 round stone. I socked the pipe just for safety measure and I also used geotextile fabric on top, so I could cover with dirt and grass. I also ordered some clay and pitched from the house to the drain.
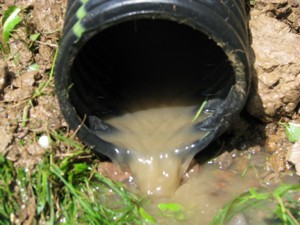
After a short rain, water is running away from the house. PHOTO CREDIT: Jim Sanders
Result? For the last month, we have had 7 or 8 torrential rains, the worst of which was last night. It rained so hard, that our lawn washed out in spots because of the high clay content. Our sump pump, that normally ran every 7 minutes during and after rain, has not turned on for 4 weeks. The silt at the bottom of the sump well is now dry and cracking. Our crawlspace has not shown a trace of water or even moisture.
Since I couldn’t see correcting the foundation cracks or the garage floor settling and tilting until I corrected the problem's source, I waited to see if the trench drain worked first.
This week, I had a company come in and perform sort of a "mud-jacking" technique on the garage floor, which worked perfectly. Also, during the past few weeks, I parged the cracks in the foundation.
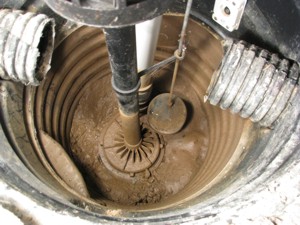
A dry sump pump. PHOTO CREDIT: Jim Sanders
I just wanted you to know how this worked. I stressed for many years over this issue and the solution was nowhere near as difficult as I thought it would be.
As a side note, I went to the end of the drain tile during a hard rain to see what was happening. Water was running out of the drain tile in about the same exact volume that it previously ran out of the weep holes in my crawlspace. This winter will be interesting, because last year, the ground next to the house was so saturated that during a thaw, my sump would run constantly. I'm guessing that the ground between the trench and the house will probably be drier now going into this winter."
- Jim Sanders, Upstate area - New York
CLICK HERE to get FREE & FAST BIDS from local drainage expert contractors.
Column QA