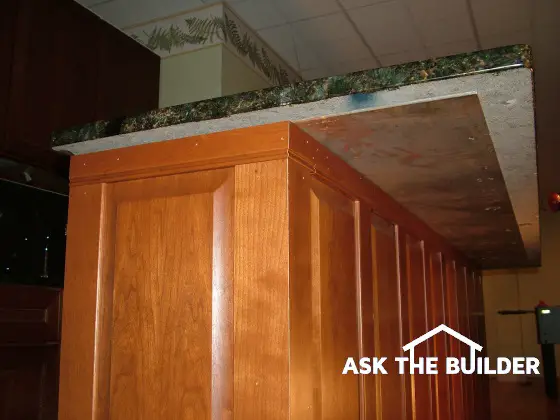
Granite Countertops | This wall assembly has two things that ensure it is strong and the countertop will not tip over; a short wall at the end of the long wall and a steel plate that supports the countertop. Some tops have granite stains caused by nature, not oil or water. PHOTO CREDIT: Tim Carter
DEAR TIM: I recently cut away the top half of an interior non-load bearing wall so I could open up the space between two adjacent rooms. I plan to put a countertop on top of the wall so we can use it for eating and a conversation center. But the one end of this new half-wall is now very flimsy and rocks back and forth. How can I strengthen this wall and how do you attach the wide countertop to this thin half-wall so that the top does not flip when someone leans on it? Mike S., Richmond, VA
DEAR MIKE: This sounds like a great project to add value to a home. Creating a pass-through space on top of a half-wall or doing major surgery as you have done really helps to make a home feel more inviting. Even if that original wall had been a load-bearing wall, the top half of it could have been removed. When faced with this situation, it is always best to hire a residential structural engineer to help create the plan for the needed structural modifications.
It is easy to understand why the end of the half-wall wobbles. Before you cut the original wall, the top of it was securely fastened at the ceiling. I am quite sure slight or moderate force at this point will cause the half-wall to bend over to the floor. If the floor beneath this half-wall is a traditional wood floor system and you can access the underside of the wood floor via a basement or crawl space, you may be able to remove the wobble in the half-wall in less than 30 minutes.
How do you support a countertop?
If you add one 2x4 stud to the end of the half-wall, making sure this stud passes through the wood subfloor and is long enough to extend to the bottom of the floor joists below, nearly all of the wobble in the half-wall can be removed. This long 2x4 needs to be bolted directly to the half-wall above the floor as well as to the side of a floor joist or to solid-wood blocking that's placed between two floor joists.
It is important for the bottom portion of this stud that is below the level of the floor to be secured at two points to the floor joist or the solid-wood blocking. This double connection minimizes rotation of the stud as a person pushes against the top of the half-wall.
If the floor is a concrete slab or you are unable to gain access to the underside of the floor, you have to strengthen the half-wall from above. This can be done a number of ways, but I prefer to add a second short wall that is oriented at 90 degrees to the half-wall. This short wall needs to be faced on both sides with three-quarter inch thick plywood that is screwed to the short wall studs. This wall also needs to be securely bolted to the half-wall. Do not nail it, as over time the nails may work loose. When you securely bolt this short wall to the floor, you will be amazed at how stiff the half-wall becomes.
Securing a countertop that is perhaps 20 or even 24 inches in width to a half-wall that is only 5 or 6 inches wide is asking for trouble. As you know, it is impractical to bolt the countertop to the half-wall from the visible finished side of the top. The connection must be done on the underside of the top.
Many builders and designers use decorative brackets that help support the top and offset the downward rotation that happens when a person pushes down against the edge of the top. I am not a huge fan of these brackets for any number of reasons. For starters, they can get in the way of peoples knees who might sit at stools as they eat or drink at the countertop. Some brackets can detract from the sleek look of the half-wall and the countertop.
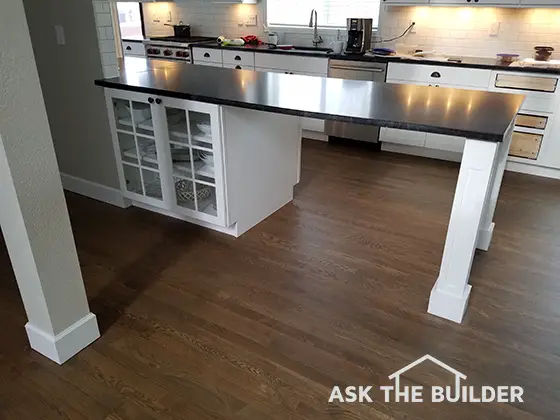
This granite top is doomed for failure the moment someone decides to sit on it unless a support is put underneath it. © 2016 Linda Hewing Perpetual license to publish it granted to Tim Carter - AsktheBuilder.com by Linda
Can a steel plate be used to support a countertop overhang?
One method that has worked well for me is to use a piece of flat one-eighth-inch-thick plate steel that is screwed and bolted to the top of the half-wall. (Refer to the top photograph.) I prefer to order the steel plate so that it is four inches less in width and length than the finished countertop. The short wall wall at the end of the half-wall becomes an ally when you use this steel support plate. When the steel plate passes over this small wall and is secured to it, it is very difficult to twist the steel plate farther down the half-wall.
Holes drilled in the steel plate allow you to place screws through it into the underside of the countertop. If the countertop is one that will not readily accept screws - such as natural stone, man-made stone or a solid-surface material, then use epoxy to adhere the countertop to the large steel plate.
The other advantage to using the steel plate is the extra strength it imparts to the finished top. If your countertop will be made from natural stone, the steel plate prevents cracks that may happen if too much weight is placed at the edge of the countertop.
CLICK or TAP HERE to get FREE QUOTES from local companies that can install your countertop so it doesn't fall.
A well-placed finished cabinet at the end of a half-wall can take the place of the short wall. The cabinet, by default, is very stable. Once the countertop is screwed to the cabinet, there is much less wobble in the half-wall. The width and depth of the cabinets helps to resist the top flipping if people push down on its edge.
When building a new home or doing an extensive remodel, the options a builder has to strengthen these long half-walls are many. Precisely placed steel angle irons can be poured into a concrete slab. Half-walls built above wood subfloors can be located so the long stud at the end of the half-wall passes directly next to a floor joist. There are often as many options as there are clever builders and carpenters!
Related Column: Granite
Column 563