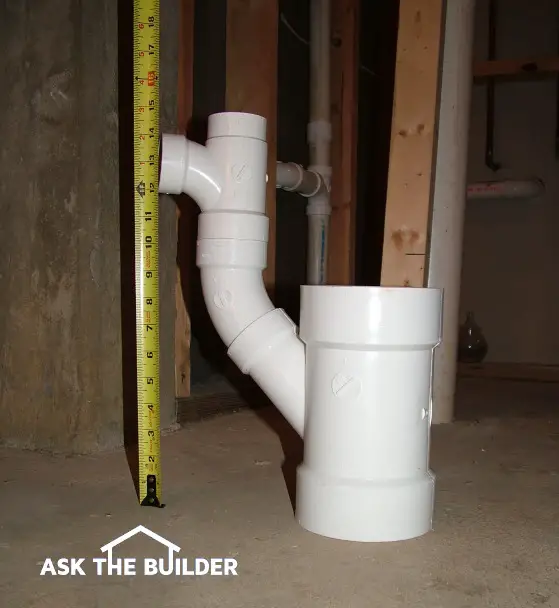
You need to assemble the new drain line fittings without cement to see how high the horizontal branch arm will be. Don't forget to account for the height of the clamp below the large 4x2 wye!
Plumbing Installation
DEAR TIM: My husband refuses to help me install a new basement laundry sink. To make it easy I have found a location immediately adjacent to a vertical plastic plumbing stack. Surely it can't be that hard to cut into the pipe and install the necessary fittings. What is involved and what do I need to do to make sure the work meets the plumbing code? Mary C., Edmond OK
DEAR MARY: What a shame your husband is not a team player. I wonder if he is intimidated by the project. There are indeed some challenges you will face, but it isn't hard to cut into the plastic polyvinyl chloride (PVC) plumbing drain pipe. The hard part is knowing where to make the cuts and making sure the new drainage branch you install is vented properly.
Why are vent pipes needed?
Just about everyone understands how water flows down a plumbing drain pipe, but what is particularly vexing to many is the need for vent pipes. When water flows from a plumbing fixture into a drain pipe, it displaces the air that moments before was in the drainage pipe system. This air must be replaced and vent pipes that extend through the roofs of house are usually the entry point for this needed air.
What happens when a vent pipe is clogged?
If a vent pipe becomes clogged or if vent pipes are improperly installed or sized wrong, the plumbing system may get the needed air by sucking it through the drain of one or more fixtures in a home. If you have ever heard a tub or sink drain gurgle or sputter when you flush a toilet, you are experiencing this siphon phenomenon first hand. When water gets sucked from a fixture trap, sewer gas or vermin in the piping system can easily enter your home. This is very unhealthy.
The first thing you must do is calculate the rough-in height off the basement floor for the center of the horizontal drain pipe that will service this new sink. You do this by temporarily setting the new sink in place and connecting the P-trap to the tailpiece drain pipe that extends from the bottom of the sink. Slide the trap up the tailpiece of the drain as high as possible so that the rough-in height of the trap outlet is as high off the floor as possible. Believe me, you will need every inch you can spare.
You will need three fittings to create the new branch drainage line: a wye, a 45 degree fitting and a tee fitting. A wye is a plumbing fitting that allows a new drain line to branch from a stack at a 45 degree angle. The size of the wye fitting will match the diameter of your existing stack. I am confident it is either a 3 or 4 inch PVC stack. Let's assume it is a 4 inch diameter plumbing stack. In this case, you will need a 4 x 2 wye as I suggest a new 2-inch diameter stack for this new fixture. In addition you will need a 2 inch street 45 fitting and a 2 x 1.5 x 1.5 tee fitting.
The street 45 fitting has a male end and a female end. The male end is inserted into the socket of the wye to create a smaller vertical secondary stack next to your existing stack. The tee fitting sits on top of the 45 degree fitting and creates the entry point for the drain pipe that extends from this new smaller vertical stack to the outlet of the trap under the sink.
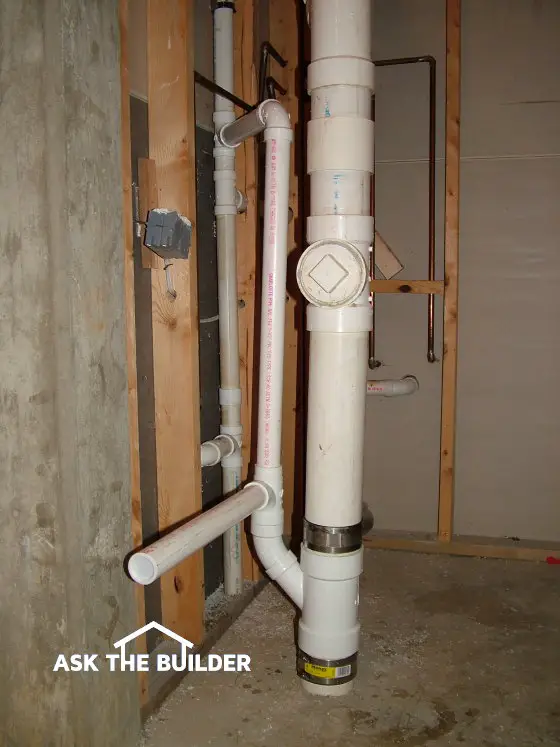
The large diameter pipe did not have the fitting close to the floor when the house was built. The extra drain line was installed to accommodate a basement laundry sink.
The top of the tee fitting is where the vent for this drain begins. A vertical 1.5 inch pipe extend up above the flood level of the sink and continues upward until it connects to another vent pipe. If you can't find a nearby vent pipe, you may have to extend this pipe all the way up to the roof. In some parts of the nation certain plumbing codes do allow mechanical vent pipes that eliminate the need for traditional vent pipes.
Can you do plumbing projects yourself?
Before you get started I urge you to check with your local plumbing inspector. First, you need to know that some cities and states do not allow homeowners to alter the plumbing systems inside their homes. Make sure you are allowed to do this job by yourself and find out about the necessary inspections. It is vitally important that you use all approved fittings, the correct clamps, the proper plastic primers and welding cements and the proper pipe sizes. The plumbing inspector can assist you with this in many instances.
If you are particularly lucky, the inspector will draw a quick diagram or make a copy of a 3-D illustration often found in most plumbing code booklets. This diagram or drawing will show you the proper pipe sizes and what the new piping system should look like once you are finished.
The weight of existing plumbing stack is significant. If this weight is not supported as the vertical stack is being cut, the piping can drop. This movement can place damaging stress on all of the piping components that may lead to leaks.
Temporary blocking and metal pipe straps and clamps can be installed to support the piping. This should be done before any cutting proceeds. The cuts into the drain piping must be square so that the new wye can be inserted with ease. If the cuts are not square, the new wye may not fit or the clamps that provide a positive seal may not fit as designed.
Watch this video to see how Tim SOLVED a problem in minutes!