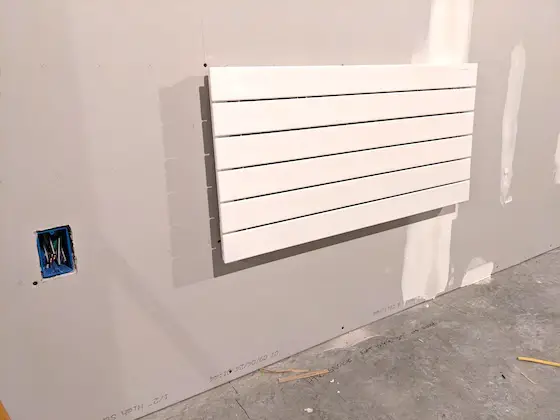
Hidden behind this 50-pound expensive wall heater are flat 2x4s nailed between the vertical wall studs. These critical framing members are blocking and ensure the heater never falls to the floor. Copyright 2025 Tim Carter
Hang a Heavy Mirror on Drywall - Blocking is Best
Have you ever struggled attaching heavy objects to a wall or a ceiling? You may employ a stud finder hunting and hoping wall studs are exactly where you need them to be. Some just throw in the towel and count on hollow wall anchors to do the job. You don’t ever have to use those when building a new home or doing remodeling.
The most recent trend over the past decade would be a flat-screen TV. These electronic marvels along with the wall-mounting bracket keep getting larger and heavier. You don’t want to hope they never fall to the ground. Kitchen wall cabinets, heavy mirrors, and paintings are just a few other things that must stay put.
Solid Wood Blocking is Best
Talk to any seasoned finish carpenter and she or he will tell you blocking is your best bet if you never want to rely on hollow wall anchors. Blocking is strategically placed wood, 3/4 of an inch or thicker, that gets covered by the finished wall covering. This wood is secured between vertical wall studs, ceiling joists, or trusses in locations where you know weeks or months from now you’ll be driving mounting screws or lag bolts.
Last year, while working on my son’s large basement remodeling project, we installed all sorts of blocking. In one instance, he wasn’t sure that early in the job the height of shelves would be in two alcoves on either side of his giant flat-screen TV. We solved this problem by installing 4-feet-tall pieces of CDX 3/4-inch-thick plywood.
CDX Plywood Works Well
This plywood was screwed to 2x2 pieces of lumber. The face of the plywood ended up flush with the face of the vertical 2x4s that created the alcoves. Months from now when the shelves are installed he can install nails or screws anywhere on the sides of the alcoves knowing he’ll hit solid wood.
We also installed critical blocking behind all of the electric wall heaters. These heaters each weigh about 50 pounds. They’re expensive and you never want them to fall to the ground. Horizontal 2x4s were nailed in between the vertical 2x4s. We referred to the heater installation instructions for guidance as to the recommended height above the finished floor for the blocking.
Shoot Photos or Videos
Not only did I take photos of the finished blocking with the centerline height above the floor marked on the flat 2x4s, but I also wrote this same information on the concrete slab with a Sharpie permanent marker. It was then child’s play to locate the center of the blocking once it was hidden from view by the drywall.
We used the 3/4-inch plywood trick in a closet under the stairs that lead to the first floor. My son wanted all of the Internet electronics, including the router, modem, and ethernet switch mounted to the wall. We laid all the components on the floor in a logical arrangement so the cables would work and be manageable. This allowed us to place the pieces of plywood exactly where they needed to be.
Our blocking mission didn’t end there, nor should yours! We had to install two rows of flat 2x4 blocking for a very expensive towel warmer in his bathroom. Once again, we didn’t want to guess the correct location. The towel warmer instructions gave a recommended height off the finished floor for the fixture.
Kitchen Cabinets Need Blocking
I’ve sworn like a sailor years ago hunting for wall studs for kitchen wall cabinets. I was determined we’d never have to do that on this job. Wall cabinets are going to be installed on a wall in his small speakeasy. Once again, we installed flat 2x4s at the correct height to match up with the inside rail at the top of the cabinets.
Blocking requires you or your builder to think ahead. This is a small price to pay in the planning phase. It eliminates frustration when it comes time to install things on walls and ceilings.
Here’s what many don’t realize about drywall. Most drywall specifications call for screw spacing to be 16 inches on center for walls. Celling drywall fasteners should be 12 inches on center.
Have you looked at how small the bugle head of a drywall screw is? Do you want to count on that to hold the drywall to the wall when you install a hollow-wall anchor? Yes, there are four screws on each wall stud. But what happens if the drywall hanger overdrives the screws and tears the facing paper? What happens if there’s a leak, the drywall gets wet, and the gypsum core turns to mush at the anchor location?
Don’t forget to take the requisite photographs or videos of the blocking before it gets covered up. Write the centerline heights of the blocking on the face of the wood with a Sharpie.
Column 1609