Hardwood Floor Maintenance TIPS
Water - Public Enemy #1
Hardwood flooring's biggest enemy is water. Water causes wood to swell. This swelling can cause warping, twisting, cupping, edge crush, etc. to occur. Sometimes the flooring will recover and sometimes it won't. The trick is to avoid introducing water to your hardwood floor.
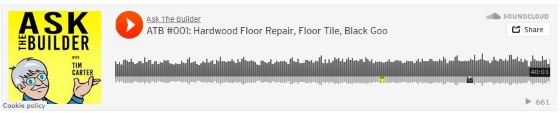
CLICK this image and listen to the first call on the podcast. I talked to Jill about how to repair wood kitchen flooring, and possibly installing an inlay border as an option. Copyright 2018 Tim Carter
Vapor Just As Bad
Water can occur either as a solid, a liquid, or a vapor. The liquid and vapor states are the ones that cause the most problems for wood flooring. Water in the liquid state is easy to see and control. It can be from a roof leak, a broken pipe, or a spill.
However, water vapor is an entirely different story. This form of water is invisible and can originate from many sources. The damage it can cause can be widespread and considerable.
CLICK HERE to get FREE & FAST BIDS from local flooring contractors who can restore your hardwood floors.
New Homes = LOTS Of Water
New home construction and major remodeling activities can create vast amounts of water vapor. Water vapor can be created by:
- curing concrete
- drying process of water-saturated rough lumber
- ceramic tile installation
- drywall or plastering activities
- painting activities
- concrete floors that lack vapor barriers
- crawl spaces that lack vapor barriers
- high humidifier settings on furnace equipment
- washing and cleaning activities
- indoor plants or large aquariums
High humidity levels in the air can not only add additional water vapor, but can also inhibit existing water vapor from dissipating.
The message is really very simple. Don't expose hardwood flooring to excessive levels of water vapor. This is especially true if you are installing unfinished hardwood flooring.
DIY No-Dust Refinish Product
Use this product to refinish your hardwood. No sanding - No dust!
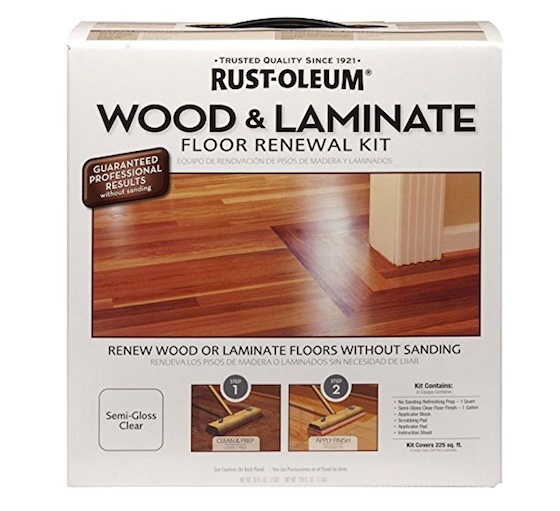
This is the wonderful DIY floor refinishing system. It's not hard to do. Just be sure the floor is CLEAN first. Use Stain Solver to clean the floor. CLICK THE IMAGE TO BUY this refinish system.
Installation Guidelines
Oak and other wood flooring materials are milled from lumber which has been kiln dried to a specific moisture content. It is recommended that this moisture content be maintained at that level for the best installation results.
That means that you should not allow the wood flooring to gain or loose any additional moisture. As such, you should not transport, load or unload the material on rainy, snowy, or excessively humid days.
The flooring should be stored in a dry, weather proof building. The storage area should be well ventilated. Never stacked or store wood flooring materials directly on concrete flooring.
Dry Flooring
The job site where the flooring is to be installed must be dry. The interior climate conditions (temperature & humidity) should be at or very near those which will be maintained during normal occupancy.
Acclimate The Wood
These conditions should begin at least five days prior to the delivery of the flooring material. The flooring material should be distributed into the rooms where it will be installed and allow to acclimate for four - five days. The interior climate conditions should be maintained at normal occupancy conditions from this time forward.
CLICK HERE to get FREE & FAST BIDS from local flooring contractors who can INSTALL your hardwood floors.
Insulate Large HVAC Pipes
If hardwood flooring is to be installed directly over the home heating plant or main duct or piping trunk lines, these lines or the subflooring should be insulated to prevent low level infra red heat from drying out the wood flooring.
Check Rough Lumber Moisture Content
Rough framing lumber should be checked for moisture content prior to flooring installation. Rough lumber can absorb vast quantities of water because of being exposed to the weather during construction. Moisture readings should not exceed 12 - 14%.
Wood On Concrete
Wood flooring can be installed on concrete floors that are on or above grade level. Installations below grade (in basements) are not recommended!!! The concrete MUST be dry.
There are several ways to test to see if the concrete is dry. The associations listed below will gladly provide you with information which will help you perform these tests.
Concrete floors must have a vapor barrier installed over them prior to the hardwood floor installation. Remember, hardwood flooring is almost never finished on its bottom side. Moisture can enter the wood from below and cause a multitude of problems. A properly installed vapor barrier will almost always stop this water vapor.
Solid Sub-flooring
Hardwood flooring must be installed on solid, approved sub-flooring materials. Non-veneered panel sub-flooring products (OSB, flakeboard, chipboard, etc.) are sometimes not recommended for use below hardwood floor installations.
If in doubt about your sub-flooring, be sure to check with your hardwood floor supplier or installer prior to the construction of your subfloor!
The organizations listed below have excellent, detailed installation manuals available. Contact them for availability. The National Wood Flooring Association, listed below, has several free pamphlets that they will mail to you concerning proper installation techniques.
Care & Maintenance of Hardwood Flooring
Never use lots of water on wood flooring to clean it. Mopping wood floors with soaps, wax removers, 'oil soaps', etc. can easily harm wood flooring. Some cleaners can leave residues which will discolor the flooring or make refinishing extremely difficult.
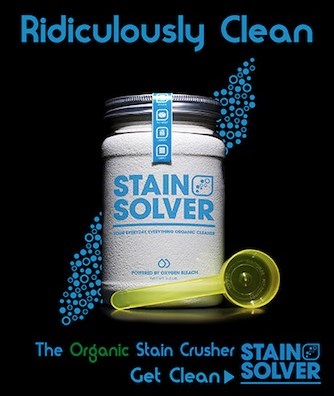
Stain Solver is MADE in the USA with USA ingredients that are food-grade quality. CLICK THE IMAGE to order some NOW.
You can clean hardwood floors using oxygen bleach like Stain Solver. The key is to just mix up a solution and use a sponge mop putting a light film of water on the hardwood.
You don't want lots of water to soak into the cracks between the pieces of the hardwood flooring.
Stain Solver is certified organic, it's Made in the USA with USA ingredients and it's a family-owned business.
Avoid Waxes and Easy-To-Use TV Products
Never use 'self-polishing' waxes, unless the product specifically states it is safe for hardwood floors. Many of these waxes contain water.
Be very careful of the miracle products heavily advertised on TV that show how a horrible hardwood floor is renewed by one swipe of a miracle liquid. It's easy to fool people on TV.
Don't over wax floors. Always try to buff floors to revive the shine. If this is unsuccessful, then and only add additional wax. Consider adding wax to the traffic areas only, not the entire floor.
Never apply a surface finish over prefinished factory materials. Prefinished products are often waxed at the factory.
Don't wax floors that have a clear or colored finish (urethane / varnish) on them. The presence of wax may make recoating extremely difficult. Clear finishes can not be applied over wax. Only apply wax to floors that you know have had wax applied from the beginning.
Remove Grit FAST
Vacuum wood floors frequently. Keep dust and grit off of floors. If you walk on grit like fine sand, you're just sanding the floor with your feet. This is a huge mistake.
Clean Spills Fast
Food and beverage residue can be cleaned with a damp (fully squeezed) cloth or sponge.
If hardwood flooring is used in a kitchen, dry mop the floor after meals to pick up any water droplets. Always use an adequate area rug in front of sinks and dishwashers. Aside from protecting the flooring, the area rug will make standing at the sink more comfortable.
Waxes Are Tough To Use And Maintain
Floors that receive waxes should be done in strict accordance with the wax manufacturers guidelines. Apply thin coats of paste wax. Remove old wax periodically with strippers that do not contain water. If these strippers contain flammable solvents, beware of explosion or fire hazards!
Add Maintenance Coat
Consider 'screening' your hardwood floors every year or every other year. This process involves lightly scuffing the old finish and applying a new, single coat of finish. If this is done on a regular basis, the floor may never have to be re-sanded and finished.
Refinishing usually has to occur if the original finish has been abused. The 'screening' process, when done by professionals, can usually be done for a fraction of the cost of refinishing. The result is a brilliant finish which looks new almost all of the time. Please give it serious consideration.
The liquid systems mentioned below yield the same results with no dust!
Old Hardwood Floor Finishes
CLICK HERE to read my column on finishing older hardwood floors.
Wood Flooring Organization
Consider contacting this organization. They offer pamphlets for proper installation, care, and maintenance. Some of the pamphlets are free. This are an extremely helpful organization.
- National Wood Flooring Association
111 Chesterfield Industrial Boulevard
Chesterfield, MO 63005
800-422-4556
http://www.woodfloors.org
CLICK HERE to get FREE & FAST BIDS from local flooring contractors who can restore your hardwood floors.
Column B114