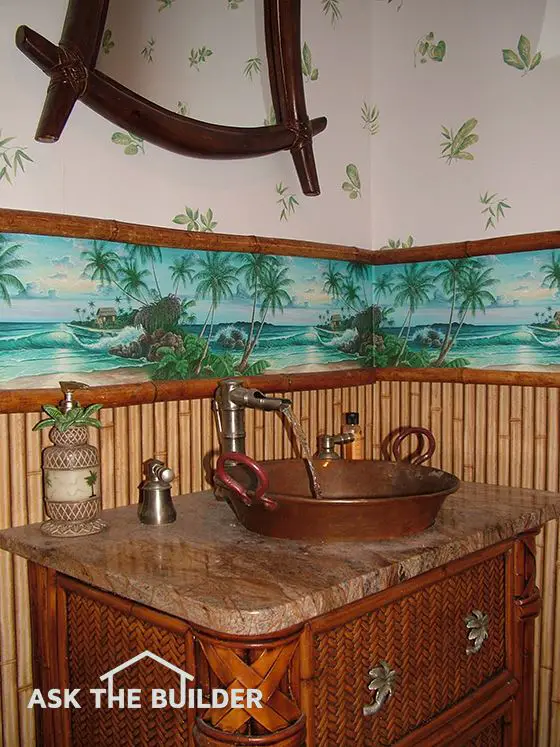
Wallpaper borders like this one with palm trees are magic. This tropical wallpaper border was easy to install. It requires minimal wallpaper-hanging skill to achieve professional results. ©2017 Tim Carter
"Wallpaper borders are a true wallpaper product, but they differ from regular wallpaper in the manner in which they are installed and their relative size."
Wallpaper Borders Checklist
- Prepasted borders are excellent choices
- Use clear paste activator instead of water
- Allow border to book for five or ten minutes
- Borders can be anywhere on a wall
Wallpaper Borders - Easy to Install & Look Fabulous
Related Links
Wallpaper and Borders on Drywall - DANGER! MUST READ!
What is Home Wallpaper? Confusion Reigns
Borders For Wallpaper
DEAR TIM: It 's time to redecorate several rooms in my home. The high cost of gasoline has put a serious crimp in my budget.
I was thinking of just painting some rooms and adding a wallpaper border for extra flair. Is this a good idea? How hard is it to install wallpaper borders?
Do I need special tools or skills? Will the borders fall off the wall in a few months if I make a mistake? Cher W. Grand Junction, CO
DEAR CHER: Wallpaper borders are a well-kept secret used by many interior decorators that I know. These simple and affordable narrow strips of wallpaper can add color and a theme to an otherwise plain-vanilla room.
Are Wallpaper Borders Like True Wallpaper?
Wallpaper borders are a true wallpaper product, but they differ from regular wallpaper in the manner in which they are installed and their relative size. Traditional wallpaper is hung vertically from the ceiling to the floor. Wallpaper borders are hung horizontally.
Traditional rolls of wallpaper might be 21 inches wide and 20-30 feet long. A wallpaper border might be 20 or 30 feet wide but only 6 to 9 inches high.
But this is perfect sizing since you want the border to dress up your wall surface in the same way as a ribbon adorns a gift box.
Free & Fast Bids
CLICK HERE to get FREE & FAST BIDS from local wallpaper hangers who can install your wallpaper border.
Where are Wallpaper Borders Installed?
A wallpaper border is commonly applied to a wall surface where the wall meets the ceiling. However, I have routinely installed a border about 36 inches high off the floor. Wallpaper borders can also be used to separate two different wallpapers in a room.
For example, my basement bathroom has a tropical-themed border that separates a bamboo wallpaper from a light-colored wallpaper that has tropical plant leaves in its background.
The border brings together two vastly different wallpapers making the three wallpaper products look like they were made for one another.
How Hard is it to Install Borders?
It's very easy to install wallpaper border material. The biggest reason, in my opinion, is that you are working with less material than a large sheet of traditional wallpaper.
Furthermore, when you do have to match the pattern, you are working with a strip of paper often less than a foot tall. This makes matching a breeze.
What Tools are Required to Install Wallpaper Borders?
To install a wallpaper border, you do need all of the same tools one uses for traditional wallpaper. Fortunately, you don't need many tools to wallpaper.
Here's a list that will get you going on this job:
- retractable razor knife with snap-off blades
- 4.5 or 6-inch drywall taping knife
- smoothing brush or plastic smoother
- 4-foot level
- grout sponge
- measuring tape
- paint roller & pan
- paint brush
Click the Image Below to get all, or some, of the tools now:
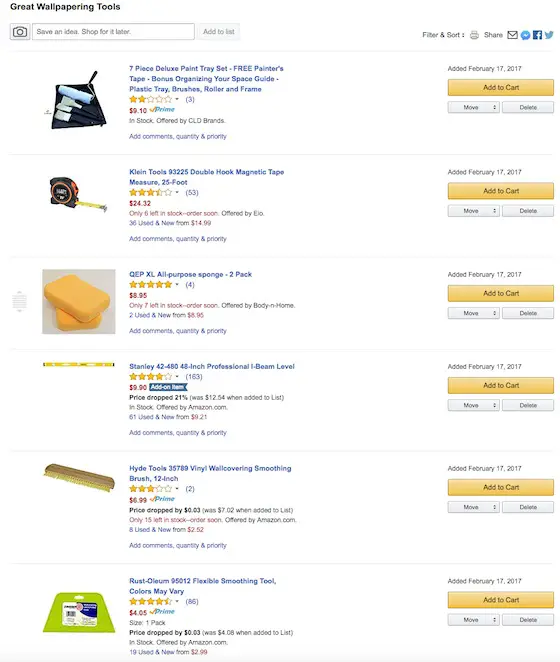
CLICK HERE to get all the tools I recommend in one place. It's easy and fast.
Do You Need a Large Table?
It helps to have a large pasting table that serves as a work platform in the event you need to apply a special adhesive or a clear paste activator gel to the back of the border.
What is the Best Border Adhesive?
If you want the border to stay attached to the wall for many years, you must pay very close attention to the type of adhesive you will be using. Some borders come pre-pasted from the factory, but that adhesive may not be suitable if you are installing the border on top of a vinyl-coated wallpaper.
In these cases, you often must use a special adhesive that bonds borders to other wallpaper products. Be sure to follow the manufacturer's written instructions, and use the correct adhesive for your situation.
Will Pre-pasted Border Work on a Painted Wall?
Yes, pre-pasted borders work very well on painted walls.
Since you are applying your border to a painted wall, and you will probably buy a pre-pasted border material, the factory-applied glue will be fine. You can apply water to the border to activate the paste, but I have had far better luck with clear paste-activating gels. These gels are quickly brushed onto the back of the border.
How Do You Hang Borders?
Hanging borders requires the same techniques one would use to hang wallpaper. The biggest mistake often made by rookies is the failure to book the border.
What is Booking and Why is it Important?
Booking is a process where you activate the paste and fold the border so the pasted surface folds back on itself. This process allows the border paper to relax. As the paper relaxes, it swells in size.
You want this swelling to happen on the pasting table while you are working with another piece of the border. If you activate the border paste, and then immediately try to hang the border, you will undoubtedly get all sorts of bubbles and blisters on the border as the border swells on the wall. This swelling action pushes the paper off the wall with each new bubble.
Should Borders Wrap Around Inside Corners?
Avoid the temptation to wrap the border around inside corners where one wall meets another. The border may look good as you install it, but hours later the border may pull away from the corner as the adhesive dries.
Run one piece of wallpaper border around the corner and trim it so there is just 3/16ths inch of border on the next wall. Then match up the pattern and start a new strip of border exactly in the corner. The second piece of border overlaps the small tab of the border from the previous strip on the adjacent wall.
CLICK HERE to get FREE & FAST BIDS from local wallpaper hangers who can install your wallpaper border.
Column 636