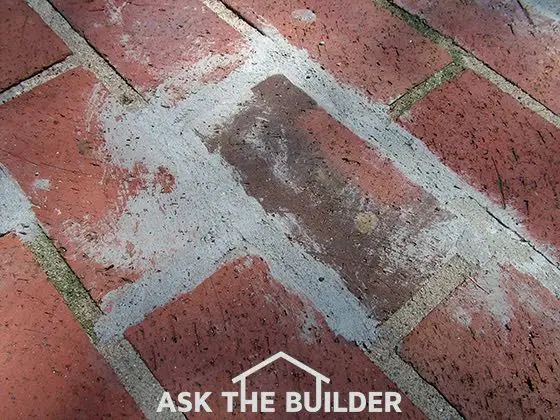
Brick patio mortar repair | This repair job could have been done with less mess, but in a week a mild acid wash will get rid of the cement stains. Copyright 2018 Tim Carter
"The first thing you need to do is look very closely at your existing mortar joints. Look at the color of the sand."
Brick Patio Mortar Repair Checklist
- Matching sand is the top priority
- Use hydrated lime in the mortar
- A mortar bag is a must-have tool
- Mortar must be rich to flow from the bag
DEAR TIM: I have a lovely brick patio that has mortar between the brick. After pressure washing it this past weekend, I noticed several locations where the mortar has disintegrated.
Most of the mortar is in excellent condition, but a few places need to be repaired. Some of the voids are 1 inch deep, while others only need perhaps one-eighth inch of mortar. How do I mix the new mortar, and what tools do I use so I don't make a mess of things? I have lots of free time, so what are the best weather conditions to work in so the repairs last a long time? Holleay P., Kitty Hawk, NC
Related Links
Matching Mortar Perfectly - SECRET Information - Do NOT Share
Best Brick Patio Repair Practices
Free & Fast Bids
CLICK HERE to get FREE & FAST BIDS from local masons who can repair your patio mortar.
DEAR HOLLEAY: Brick patio designs are as plentiful as blossoms in spring, but a traditional brick patio that has been mortared in place is one of my personal favorites. These patios are like a brick wall that is lying flat on the ground, and the mortar becomes an interesting design element because of its texture and color. I have two brick patios just like yours, and they get compliments each time a friend or neighbor sees them for the first time.
What is the Best Brick Patio Mortar?
The best brick patio mortar, in my opinion, is one that contains hydrated lime, Portland cement, and a medium sand.
When I am building a brick patio like the one you and I have, I use a special mortar that will withstand years of Mother Nature's abuse.
It sounds like your builder did the same thing, but the mortar in a few locations was defective. That has happened to me in a few spots on my own patio. I traced the defects to excessive water from a rainstorm that happened soon after one section of the new brick was grouted.
What is the Best Mortar Recipe?
I suggest you repair the defective joints in your patio with the same type of mortar mix I used when I installed my patio. It's extremely durable, and will last for 40 - 50 years if you cure the joints once they are installed.
- three 5-gallon buckets of dry sand that matches existing sand in patio mortar joints
- 6.38 gallons of Portland cement
- 1.12 gallons of hydrated lime
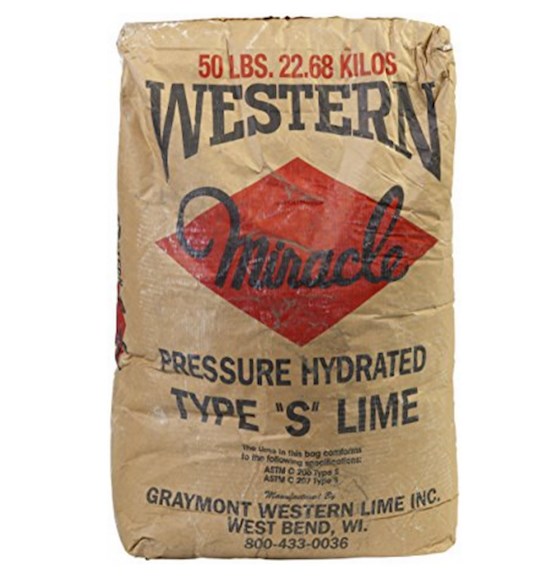
This is excellent hydrated lime. It's a fine white powder and it's going to look great on your home. CLICK THE IMAGE TO ORDER SOME RIGHT NOW.
How Do I Match the Sand for the Mortar?
You match the sand by paying attention to the color and size of the individual pieces of sand in the old mortar.
Your biggest challenge is going to be matching the color and texture of the existing mortar. You did the right thing by thoroughly cleaning the brick and mortar first. All too often, people try to match mortar colors and fail to clean the surrounding mortar first. Mortar on walls, and especially on flat patios, can get very dirty.
The first thing you need to do is look very closely at your existing mortar joints. Look at the color of the sand.
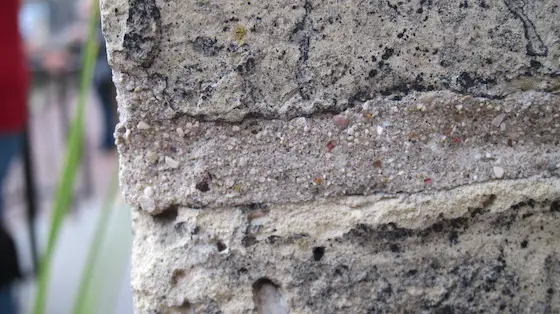
Look at the colored pieces of sand. Note the size and different colors. I see white, black, orange, and some gray pieces of sand.
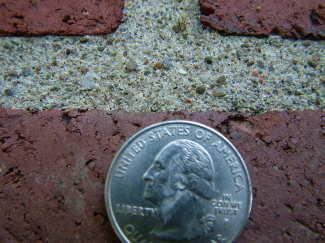
Check out the different colored pieces of sand. Each grain is a small piece of solid rock. The sand for the repair job should match the existing sand as close as possible in grain size, shape and color. Copyright 2018 Tim Carter
Is All Sand the Same?
Believe it or not, not all sand looks the same. Sand is simply a collection of very small rock particles, and the color of individual sand particles can be vastly different if the particles come from a variety of black, red, white and gray rocks. Visit different building supply businesses and/or sand and gravel pits, and try to find sand that matches both in color and particle size.
Once you have the correct sand, mix your brick patio mortar using my recipe you see above. This will make a very rich mixture that will be exceedingly strong.
You need this strength, even though you do not get too many extremely cold days.
CLICK HERE to get FREE & FAST BIDS from local masons who can repair your patio mortar.
What is the Best Tool to Install the Mortar?
A grout bag is the best tool to install the brick patio mortar.
Extra cement and hydrated lime in your mortar help make the mortar flow easily from the tip of the special grout bag you'll use to fill the defective mortar joints.
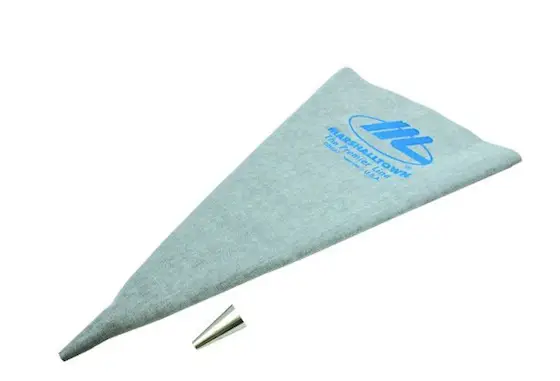
This is a great mortar repair bag. I own one and it's installed thousands of feet of mortar into joints. CLICK THE IMAGE NOW to have one delivered to your home.
Mortar grout bags are just like icing bags used by professional cake decorators. They are larger than an icing bag, and have a metal cone tip that has a one-half-inch hole at the end.
What's the Best Weather to Repair Brick Patio Mortar?
I prefer to work on cloudy days when the temperature is in the 50 - 65 F range. Do not work on a hot, sunny windy day. The mortar will dry too rapidly, especially where you are filling slight depressions in the existing mortar joints.
How Do You Install the Mortar in Between the Brick?
Once you have the mortar mixed, lightly spritz the mortar joints you are going to fill. Do not get them too wet, just slightly damp.
Fill the grout bag half way with the mortar mix, and apply slight pressure to make the mortar mix flow just as toothpaste oozes from its tube. If you can't get the mortar to flow, you need to add more cement and/or slightly more water. The mortar mix needs to be fairly wet so that it doesn't clog the grout bag tip.

These deep joints can be filled with new mortar using the special grout-bag tool. Once the mortar is stiff, scrape off excess with the small trowel. Copyright 2018 Tim Carter
Carefully guide the grout bag tip so that you apply new mortar only to the joint. Move the bag along and make sure you apply mortar so it rises above the level of the brick by about one-quarter inch.
The fresh mortar needs to touch the top edges of all the brick. Let it set until you see it change from wet and glossy to a flat gray color. Use a small triangular trowel to gently scrape off the excess mortar so the top of the mortar is flush with the brick. Keep the fresh mortar damp for three days so it cures well.
When Do You Scrape Off Excess Mortar?
If you scrape the excess mortar too soon, it will smear onto the brick. You do not want this to happen, especially if the brick has a rough texture or grooves created by the wire-cutting process as the brick is manufactured. If mortar gets in these grooves, it is a nightmare to remove.
You also have to be careful about waiting too long to scrape off the excess mortar. If the mortar gets too hard, you run the risk of breaking the bond between the new and old mortar. If this happens, your new mortar may fail in a few years.
CLICK HERE to get FREE & FAST BIDS from local masons who can repair your patio mortar.
Column 621