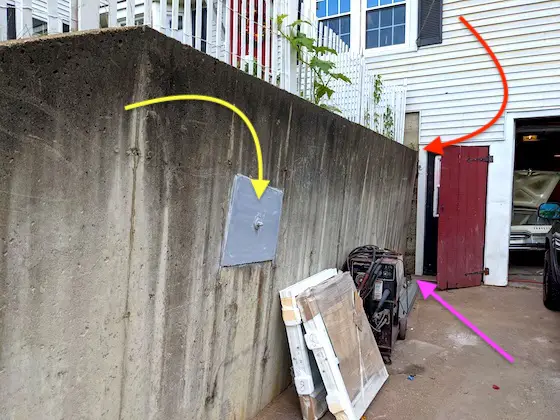
This retaining wall is failing. The top is tilting to the right. It's already moved about 10 inches out of plumb. Note the amount of house foundation exposed between the red arrow tip and the magenta one at the bottom. The yellow arrow points to a gray steel plate was added as the wall started to tip over. It's an attempt to stop or slow the wall from tipping over. The bolt in the center of the plate connects to a thick rod that extends back into the soil behind the wall. There's another plate in the soil at the other end of the buried rod that is acting like a boat anchor. You can only tell if it's working if you start to take measurements up by the tip of the red arrow. Read below WHY the retaining wall FAILED. It's all about levers.
Retaining Wall Types - Tall Walls Can Be Trouble!
Retaining walls require thought and planning just like any other building project. Soil properties, drainage, surcharge loads (additional weight from objects placed on top of the ground above retaining walls such as cars and trucks), height of the wall, bedrock geology, etc. all must be taken into consideration.
It really pays to do your homework, due to the amount of work and cost in building a retaining wall. Many fine publications are available that offer suggestions and design tips in constructing retaining walls. Several are listed at the bottom.
Many of us live in parts of the country that are not so level. The geography and topography can range from slightly rolling to mountainous. Those of us who do live in these regions are quite familiar with retaining walls.
What Do Retaining Walls Do?
Retaining walls allow us to create steps or level areas on a sloped surface. However, if constructed improperly, the forces of nature (gravity, water, etc.) will topple a retaining wall in short order.
Retaining walls have been in use for thousands of years. The Romans used retaining walls to aid in the construction of their famous roads. Many of the castles in Europe incorporated retaining walls into their design.
Hillside rice paddies in Asia have depended on retaining walls for hundreds of years. Trial and error construction methods of the past and advancements in engineering knowledge have indicated that four basic types of retaining walls seem to perform quite well.
What are the Four Types of Retaining Walls?
Gravity Walls
A gravity retaining wall is usually a low height (less than 3 to 4 feet) wall that depends on its own weight or mass to hold back the earth behind it. This goal is achieved by constructing the wall with a volume of material so that when stacked together, the weight and friction of the interlocking material exceeds the forces of the earth behind it.
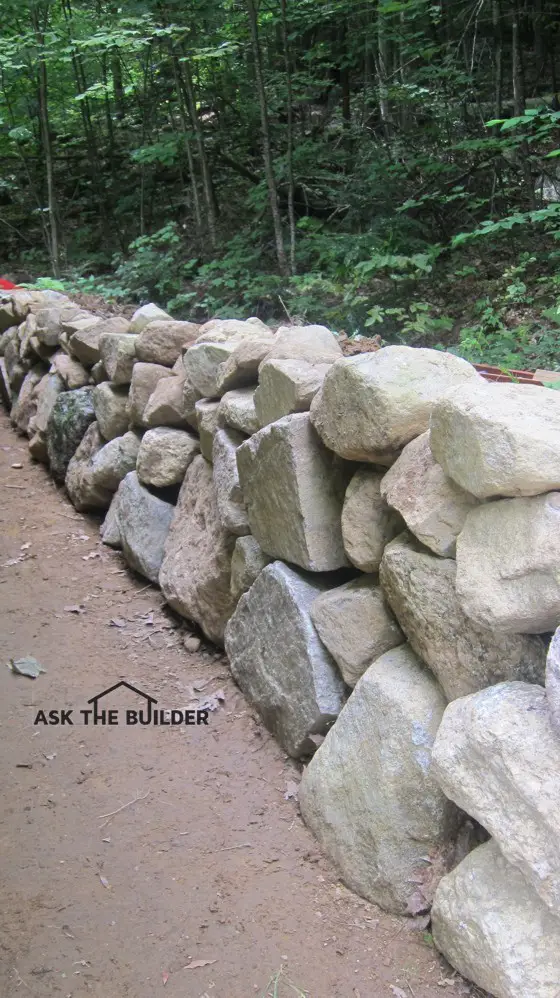
Gravity Retaining Wall - This is a perfect example of a gravity retaining wall. It's about 30 inches tall. Most of this rock wall was built in less than five hours by one person. Some of the larger rocks had to be put in place with a machine. Copyright Tim Carter 2021
The gravity retaining wall is thicker at the base than at the top. Also, note that as the front of the wall gets taller it slants backward. This is often referred to as 'battering'.
This battering effect creates a visual message of strength. Over time, the wall may succumb to the forces of gravity and begin to tilt outward. By battering the wall backward, you extend the visual life of the wall. Retaining walls that appear to be tipping over, indicate faulty construction and impending failure.
Walls that are battered send a visual message that the wall is 'working' and that it is continuing to beat the force of gravity. Gravity walls become very cumbersome to construct as they get higher, because they require vast quantities of materials.
How Thick Should A Gravity Retaining Wall be at its Base?
The thickness of a gravity wall at its base should be one-half to three-fourths its height. So, if you intend to build a wall 4 feet high, the base should be 2 to 3 feet wide. As the wall gets higher, it begins to get thinner.
CLICK HERE to get FREE & FAST BIDS from local masonry contractors who can build your new retaining wall.
Cantilever Walls
A cantilever retaining wall is one that consists of a uniform thickness wall that is tied to a footing. A cantilever wall usually is asked to hold back a significant amount of earth, so it is a good practice to have these walls engineered. A simple example of a cantilever retaining wall is a typical basement wall of a house.
The width of the footing for a cantilever wall is very important. The footing is designed to resist tipping or sliding forces which the earth exerts upon the wall. Also, the wide area of the footer allows the weight of the earth to actually keep the wall from tipping in some instances.
These walls require significant steel reinforcing in both the footer and the wall structures. The steel also has to extend from within the footer up into the wall so that the two pieces actually become one integral unit.
As you can see, this is why these walls need to be designed by structural engineers. If you try to guess yourself at the amount, size and placement of structural steel in this type of wall, you are gambling.
Also, the thickness of both the footer and the wall is extremely critical. Don't be a fool and try to become a weekend engineer. Spend several hundred dollars and get it right the first time!
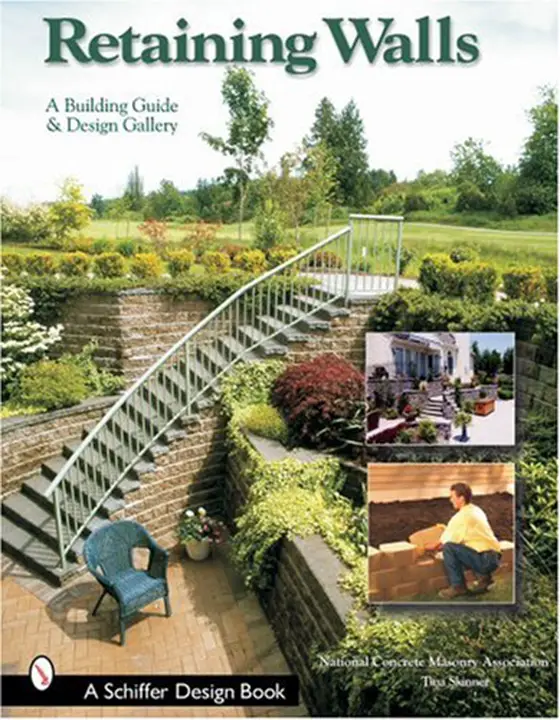
CLICK THE IMAGE to get an essential guide on building retaining walls for whatever situation you may be dealing with.
Counterfort Retaining Walls
A counterfort retaining wall is very similar to a cantilever wall, except that it has one additional feature. This wall has a triangular shaped wall which connects the top of the wall to the back of the footer.
This added support wall is hidden within the earthen or gravel backfill of the wall. The footer, retaining wall and support wall must be tied to one another with reinforcing steel.
If the structure is poured concrete, often the retaining wall section and the support walls are poured as one unit at the same time. The support walls add a great deal of strength to the retaining wall.
The supports make it virtually impossible for the wall to become detached from the footer. As with cantilever walls, a counterfort wall should be designed by a competent structural engineer.
If you decide to attempt to construct this type of wall without approved plans, you are making a huge mistake. If the wall fails, the cost to remove the failed wall, construct the new one, etc. could be ten times or one hundred or more times the cost of engineering services. Remember, engineers have to eat just like you and me!
Buttressed Retaining Walls
A buttressed retaining wall is basically identical to a counterfort wall except for one thing. The support wall is on the outside of the retaining wall. They are visible. The buttresses add incredible strength to the wall system.
For the retaining wall to fail or tip over, the buttresses would have to be crushed. The buttress concept was widely used in the construction of many cathedrals in Europe.
Because of the height of the cathedral walls, the buttresses helped to stabilize them. They do the exact same thing in a retaining wall. Once again, if you intend to build one of these walls, you must give serious consideration to hiring an engineer.
Situations which demand this type of wall usually have tremendous loads which bear against the walls. The buttresses can often be designed to be decorative in nature and covered with stone or some other material.
Depending upon the overall length of the wall, you may have several buttresses. They can be spaced to create rooms, parking spaces, handball courts or any other functional space. Use your imagination!
CLICK HERE to get FREE & FAST BIDS from local masonry contractors who can build your new retaining wall.
Retaining Walls - Books & Publications
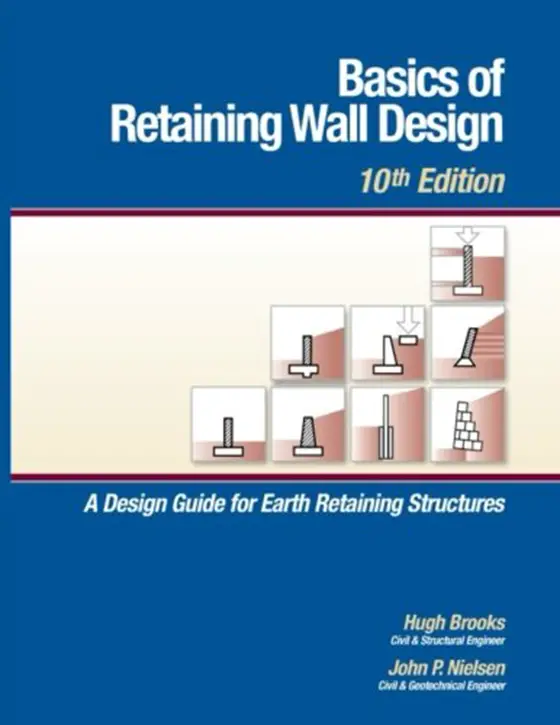
CLICK THE IMAGE to view a wide selection of books and guides on how to build, drain, and design retaining walls.
Retaining Walls are Levers
Think of how a lever works. It's a long pole that you push down or up on one end. In a simple lever situation, the greater the distance between the fulcrum, the pivot point, and the item being lifted or pushed, the LESS force you need to impart on the lever to get the object to move.
Retaining walls are levers. The taller the wall, the less force it takes at the top to push it over. See why you should have paid attention in high school physics class?
If you decide to construct a wall over 3 feet tall, give serious consideration to hiring an engineer to help you in the design of the wall. Many engineers often have designs they have created for other walls in your area. They do not have to start from scratch.
Often they have to perform various simple calculations to ensure that the design will work in your instance. This service may only cost $200 to $500 dollars. That is a small price to pay for a wall that will not fail.
CLICK HERE to get FREE & FAST BIDS from local masonry contractors who can build your new retaining wall.
If you do obtain a plan or design and hire a contractor to perform the work, inspect the work daily to ensure that the wall is being constructed as the engineer intended. Take photographs of the steel before it is covered with concrete.
Document everything! Be careful not to backfill the wall too soon!!! Masonry (block, stone or concrete) walls take a while to develop their strength. Often it takes weeks! Your engineer will tell you when it is safe to fill behind the wall.
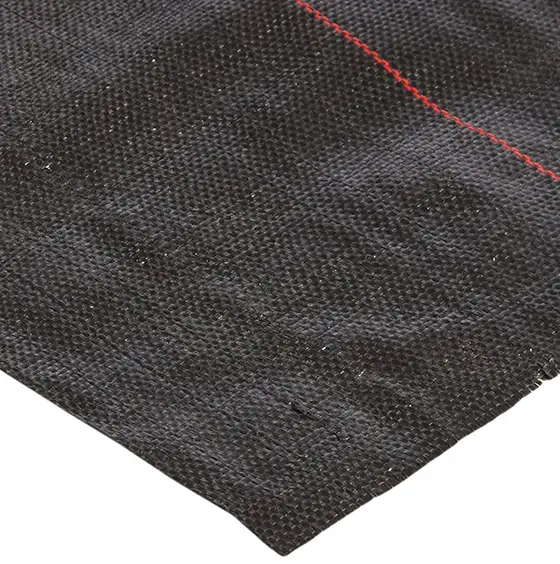
CLICK THE IMAGE to get a woven geotextile that will keep soil in place.
Pay particular attention to drainage behind the wall. All walls should be backfilled with coarse gravel that drains quickly. Water must be able to drain from the back of the wall. Water is extremely heavy.
If water is allowed to collect behind the wall, it just adds additional pressure which may cause the wall to fail!! Be sure to account for water drainage. Install a drain tile behind the wall at its base. Provide holes in the wall to allow water to easily flow to daylight. Do whatever it takes to get water away from the wall.
Column B37