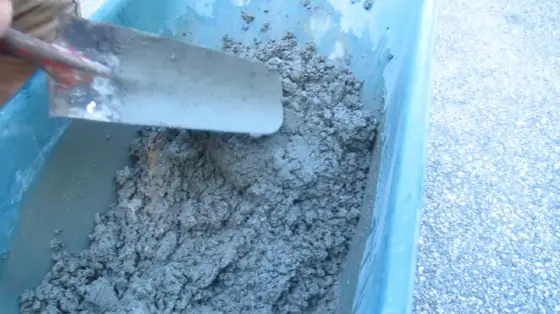
Here’s some concrete in a wheel barrow that’s been mixed by hand and it nearly perfect in consistency. Photo Credit: Tim Carter
Concrete installation is not easy. The material is heavy and you only have a limited amount of time to finish it to get great results. Adding water to it at any time after it's mixed increases the chances of failure.
Revised February 2018
Concrete Is A Magical Material
Concrete is a remarkable material. It's important to realize it's man-made artificial rock.
Think about how this material that once mixed has a plastic consistency like pancake batter and hours later it's hard. A month later it's so hard it can support a skyscraper!
Concrete technology is, in fact, a science. There are scientists who devote their entire life to working with this material. These people research methods to improve it and its use.
My guess is that just about everyone has seen concrete being poured. Concrete begins its life as four basic ingredients:
- sand
- gravel
- Portland cement
- water
These are blended in precise quantities so it has the consistency of pancake batter. It's a plastic material at this stage.
Related Links
Secret Recipe for Long-Lasting Concrete
Special Tricks for Installing Concrete in Cold Weather
This concrete mix transforms into a solid material usually within a matter of hours. The length of time depends primarily on the temperature of the mix, the outdoor air temperature, and the amount of direct sunlight striking the concrete.
I must tell you that each and every time I work with concrete I marvel at this transformation.
Free & Fast Bids
CLICK HERE to get FREE & FAST BIDS from local concrete contractors.
Crystals Grow During Concrete Installation
If you know how and why concrete transforms from the liquid to the solid state, you'll more easily understand why concrete fails or experiences surface defects.
The Portland cement powder is the glue that holds the sand and gravel together. An irreversible chemical reaction called hydration starts to happen when water is added to the dry powder.
This reaction causes tiny crystals to begin to grow. The crystals act like Velcro® and lock together the tiny grains of sand to the pieces of gravel. This reaction continues for months after the concrete is initially mixed.
The needles of the crystals begin to interlock with one another and begin to penetrate microscopic holes and cracks in the sand and gravel. The crystals cement everything together. No pun intended!
Concrete Stiffens Within Hours
The growth of the crystals can be monitored. If you have ever had the pleasure of working with and finishing concrete you can feel the crystals growing. As each minute or hour passes after the concrete truck has left the job site, the concrete becomes progressively stiffer. It soon gets to a point where it will support the weight of a person using an automatic finishing machine. The growth of the crystals allows this to happen.
Things can go wrong if the crystals grow too fast. For example, you may not be able to achieve the desired finish because the concrete gets too hard to fast to put on a desirable top finish. Hot weather is the most common reason the crystals grow faster than you or the finisher would want to have happened.
If you're pouring concrete in hot weather, you have to have plenty of finishers on the job to ensure the concrete doesn't get hard before it's finished.
You can add special chemicals to the mix to slow down the hydration reaction.
CLICK HERE to get FREE & FAST BIDS from local concrete contractors.
Concrete Surface Defects - Some Common Causes
Concrete surface defects are often caused as the crystals begin to grow. One of the biggest reasons for surface defects is the addition of extra water to the mix and/or the use of water on the surface of the concrete as a part of the finishing process.
Both of these practices are frowned upon by concrete scientists. The reasons are numerous, however, they all have to do with those silly cement paste crystals.
Water is the Friend and Foe of Concrete
Water is frequently added to concrete after it arrives at a job site. Concrete finishers often will look at the batch as it begins to discharge from the concrete truck.
They may think that it is too stiff. The addition of extra water makes the concrete flow easier. There will be less work. They think they will have more time to finish the concrete.
Concrete was initially mixed at the concrete plant has plenty of water. In fact, as long as accepted work practices are used in placing and finishing the product, the concrete has extra water. Professional installers who use slip-form equipment to pour barrier walls and concrete curbs in new subdivisions use concrete that's got so little water in it, there's no need for wood forms to hold its final shape.
Watch these two videos to see proof of this. Regular concrete finishers could never work with this material by hand because it's far too stiff.
Water Is Lightest Of The Four Ingredients
You can actually observe this fact if you pour concrete on top of a plastic vapor barrier. Frequently, after the finishers have bull-floated the concrete to smooth it initially, water migrates to the surface of the slab. This is called bleed water. It comes to the surface because it is actually the lightest component of the entire batch!
The addition of extra water at the job site alters the chemistry of the crystal reaction. The cement paste is severely diluted. The cement particles are farther apart from one another and not as many crystal needles interlock.
The concrete will be weaker if you add extra water. The addition of extra water during the finishing process produces the same results, however, just the top layer of concrete is usually affected.
Water is often added by finishers because the concrete is getting too hard to finish. The growing hydration crystals will be broken apart if you add water to the top surface at this time. The addition of water allows the finisher to more easily work the surface of the concrete.
It's a mistake to allow this to happen. You prevent this by having enough workers finishing the concrete so no water has to be added.
Another key point is the entire batch of concrete is mixed at the same time. This means the hydration crystals are growing at the same rate throughout the mix.
Remember, if you are finishing a large slab alone, the crystals are growing everywhere across the slab!
CLICK HERE to get FREE & FAST BIDS from local concrete contractors.