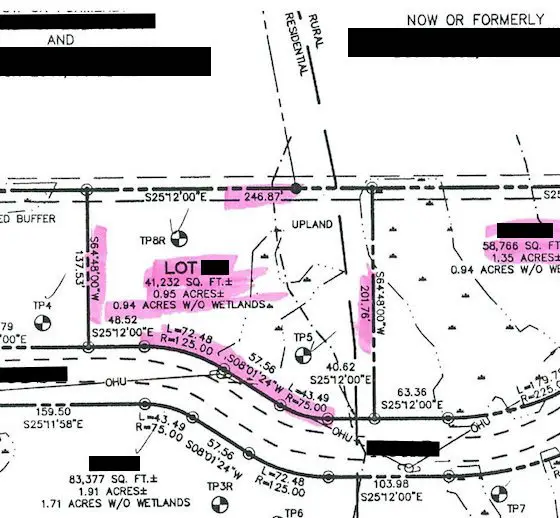
This is a typical plot plan survey document. You can see the property lines, the pins at all the corners and bends as well as the distances along the property lines. Don't even look at a lot unless you have this in your hands and you can read all the print on the document. Copyright 2018 Tim Carter
See Part I of "Lot Selection- 25 Tips"
See Part II of "Lot Selection- 25 Tips"
Water
Do you need water at your site? Do you intend to drill a well? What will it cost? Is the water pure? Wells can be expensive. The water may be salty or have a high mineral content. Ask neighboring lot owners, if any, how their water is. Talk with local drilling companies and obtain cost estimates.
The best wells are ones that are pounded, not drilled. Drilling can sometimes fill the cracks in the bedrock that are the pathways for water to enter the well. Pounding a wall helps create more beneficial cracks.
Survey
Buying any property without a registered house lot survey is insane. Negotiate for the seller to pay for the survey. It is NOT unreasonable, since he/she should have to prove to you what you are going to get in the deal.
Only fools buy on the HOPE principle. Don't "hope" that your lot line is over there or that you really have 10 acres and the creek is on your property.
Free & Fast Bids
CLICK HERE to get FREE & FAST BIDS from local land surveyors who can show you your exact land!
Access
Is the access to your lot excellent? Do you have to build a long, expensive driveway? Do you have to cross a stream? Will a fire truck, or moving van be able to get close to the house? Maybe access is too good. Maybe the lot access is too close to an intersection. What about adjoining land? Will you have to give access across your lot to logging companies who will timber Federal Lands next to yours? Trust me, you wouldn't be the first.....
Common Roads - Undedicated
Do you have to share a common roadway or driveway with access to another lot or a group of lots? This can be a nightmare. What happens if you are the first to build and subsequent construction activity ruins the road or driveway? Who pays? What happens if you want to seal the blacktop and your neighbor doesn't?
Panhandle or Flag Lots
These are what I call back lots. A narrow strip of ground allows you to get to and from the street. These lots can be mistakes. Utility trenches may end up beneath the drive. Your front yard may be in someone's backyard. I haven't seen a good one yet, but I'm still looking.
If you can't resist buying a flag or panhandle lot, be sure the handle or flagpole section is at least 40 feet wide. This gives you room to bury utilities on the sides of the drive and to plant some privacy bushes.
Easements
An easement is a legal permission slip, often permanent, which allows someone else to cross your land in a certain spot.
In certain instances, depending upon the type and size of the easement, it can be a BIG MISTAKE!
The lakefront house I owned in New Hampshire had an easement across it allowing my neighbor to drive up to the cul de sac. It's important to note that I had an easement across a portion of his land so I could get to the cul de sac as the top section of our driveway is shared.
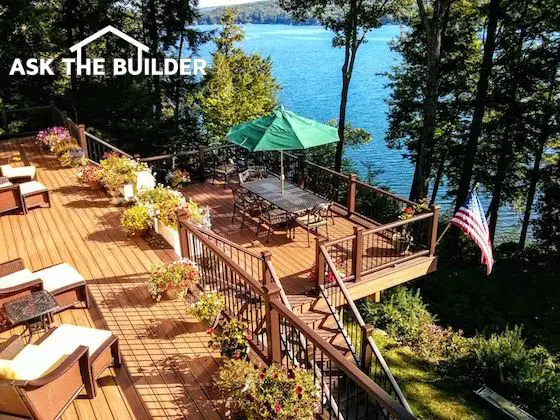
Here's my own Trex Transcend deck. There's lots of railing. It didn't take long to understand how to do it with professional results. Copyright 2017 Tim Carter
Try to avoid lots that have easements. If you must have one, try to see if it can be on one edge of the property, not through the middle.
By all means purchase Owner's Title Insurance with your land. The title insurance policy can protect your investment should some future easement or title flaw come out of nowhere in the future.
Mineral Rights
Yes, your lot may have mineral rights! There could be oil or some other commodity product such as gravel near or beneath your lot. A friend of mine found out that his country lot was going to be next door to a brand new gravel pit. Now that could really ruin your day....
Tax Rates
Be sure to investigate the tax rate for your lot. Is it reasonable? How will improvements on the lot be taxed? If the land is currently zoned agricultural, it may have an artificially low rate. Once improved, you may lose the agricultural tax rate. Check with the local tax authority.
Encroachments
Guess what? Your fence might not be yours. In fact, your house might not be yours! It has happened. In fact it happened to me! Using stakes set by a surveyor, I once built a commercial building on someone else's land by 1 foot! It cost the surveyor $25,000 for a 2 foot by 100 foot piece of land! Encroachments can be expensive to fix. Attorneys almost always have to get involved to separate the legal issues. A survey performed before you buy will usually reveal them, but, as in my case, it is no absolute guarantee.
CLICK HERE to get FREE & FAST BIDS from local land surveyors who can show you your exact land!
Column B154