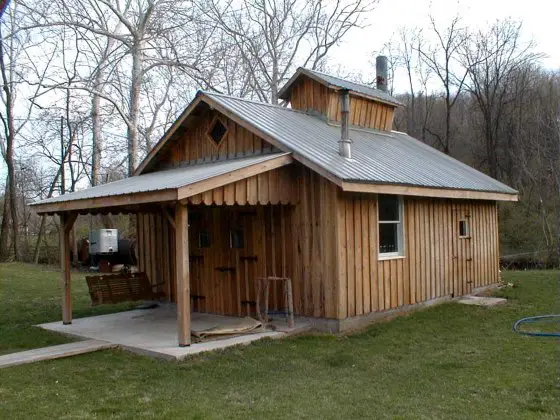
I helped build this unusual cabin-like structure. It is a shed for distilling maple sap into maple syrup. Would you believe it if I told you it was less than seven miles as the crow flies from downtown Cincinnati, OH?
DEAR TIM: I am going to build a cozy cabin on some property I have in the woods. I would like to have a wood stove in it for heating purposes. What is the smallest size you think I can build and have many of the creature comforts I have in my existing home? If you could have the cabin of your dreams, what size would it be and what features would it include? John M., Neenah, WI
DEAR JOHN: Oh, this sounds like a dream project if you ask me! What a delight to be deep in the woods framing this cabin. I have spent time in several different cabins and know what a blissful time you are going to have sitting on its covered porch on those late summer evenings. I'm just about ready to trade some labor for periodic vacation visitation rights.
The biggest design constraint, in my opinion, is the minimum number of people that are possibly going to sleep in this cabin at any given time. Beds or cots take up an enormous amount of floor space when you are talking about small cabin and cottage structures. Don't try to plan for people to sleep on the floor. It is impractical, uncomfortable and can cause enormous traffic flow problems if the person(s) on the floor is still sawing logs while other inhabitants are trying to move around.
If you feel that more than two people are going to sleep in the cabin at a time, then you need to consider building a cabin that has a cozy sleeping loft. The loft space is created easily if the roof of the cabin has a steep pitch of 9 inches of rise for every foot of run (9/12). If you increase the pitch to 12/12, you can almost create a loft that has 8 feet of ceiling height in the center of the loft.
The smallest cabin foot print I feel that is workable is one that is 16 feet wide and 12 feet deep. Add to that a covered front porch that is 16 feet wide and 6 feet deep and you will have a little gem. A small cabin like this will accommodate a standard bed in one corner, a large chair in another corner, and a toilet and shower and kitchenette in the remaining corners. You can place a stove in the center of the cabin for even heating if you want, but its chimney will pass through the center of the sleeping loft. I feel that cabin stoves work best on exterior walls.
Let's see, the cabin of my dreams. I don't want my cabin to be too large because then it isn't a cabin but more like a small house. I feel an ideal size is one that is 20 feet wide by 18 feet deep. It would have a 12/12 roof pitch and nine foot high walls that would provide a very spacious feeling. The sleeping loft would just be above the center core of the cabin so that the underside of the roof was visible along all of the exterior walls. A guardrail wall would surround the loft on 3 sides for privacy and safety purposes. It would easily stop a restless occupant from crashing to the lower floor in the middle of the night.
My cabin would be constructed with 2x6 walls and 2x12 floor joists to allow for maximum insulation. I would place a vapor barrier on the bottom side of the joists to make sure the cabin didn't get musty. Since I prefer lots of light, the windows would be a minimum of five feet tall and have very few, if any, mullions in the sashes. When inside, I would want to enjoy as much of the outdoor view as possible. The exterior door would be an insulated steel door with top of the line weatherstripping.
The cabin walls would include an air and water barrier wrap before the siding would be applied. This will help to minimize heat loss which means I would have to split less firewood. The interior walls would be wood covered and stained and sealed so that they are light and airy. I want the interior of the cabin to be bright at night. Keep in mind that most woods develop a patina over time and they naturally darken. A medium colored wood can become dark in less than 10 years. My cabin would have the best wood stove available. It would be equipped with a cooking surface and hopefully have space for an old fashioned Dutch oven. Because of my love of natural light, I would try to include at least 4 skylights. I would make sure that these could open slightly so that they would provide some wonderful up-flow ventilation on those balmy summer days.
Column 313