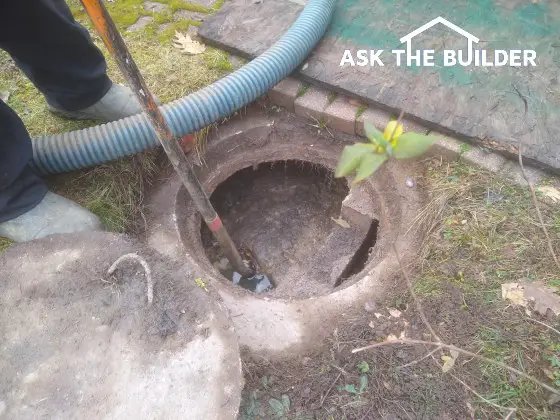
Septic Tank Maintenance - This is a septic tank about to be pumped. It’s a best practice to do this every two or three years. Copyright 2024 Tim Carter
Septic Tank Maintenance
This past Saturday, a very good friend of mine was at my house. I call him Yoda, as he is my computer guru. He was helping setup a new computer for me. At lunch, we were talking about a problem he had at work. Mind you, I didn't bring this subject up. An employee had flushed a toilet and water backed up into a floor drain on the warehouse floor. To make a long story short, the septic system had failed.
When the service company arrived, they asked where the septic tank was located. No one knew! The septic system had never been serviced. Oh well, there go this year's Holiday bonuses!
Septic Tanks are as Good as City Sewers
Septic systems suffer from an inferiority complex of sorts. City folk scorn them thinking that they are just one step removed from an outhouse. Nothing could be further from the truth. Septic systems which are designed, installed, and operated properly treat wastewater as well as any municipal sewage system. In fact, some septic systems do a much better job!
Septic systems also receive bad press in response to claims of groundwater pollution. Yes, it can happen. However, many of these instances can be traced to substandard maintenance on the part of the homeowner or bad initial design. The septic tank and drainage field can do its job, you simply need to be a part of the team!
High Upfront Cost - Forty Cents a Day to Maintain (2024 prices)
Septic systems are very cost-effective. Yes, there is a sizable upfront cost to install a complete system. However, once installed periodic inspections and pumping charges should be your only expense.
People who have public sewers pay for these systems. They are taxed monthly or quarterly. Here in Cincinnati, our sewage bills are directly related to our water bills. If you use lots of water, you pay a proportional upcharge for your monthly sewage use. There are no free rides. A simple analysis would show that many homeowners on public sewers might actually pay more on a monthly basis than septic users.
Well-Drained Soil is Key
Septic systems take advantage of the natural cleansing properties of soil. Soil and the microbes it contains can act as an extremely efficient biological eating machine. However, if the soil is waterlogged or has low permeability the wastewater can migrate to another location before it has been converted to a harmless state.
As such, a simple study needs to be completed to evaluate how well your soil drains. Virtually every county in every state has a Board of Health official who performs this task. If they don't perform it, they will direct you to the proper authority, such as the local plumbing inspector. Just about every home building site that has a large enough lot can be adapted for septic use. Hillsides, wetlands, rocky areas, etc. all can be modified for successful septic system installations. The Basic System
Septic systems are really simple when you think about it. Most systems consist of two major components: the septic tank and the drain field.
The tank is a large vessel buried underground. They come in different sizes. The size is directly related to the number of occupants in the house or structure. The tank does two very important jobs. It acts as a settling basin and starts the process of waste decomposition. When you send wastewater towards the tank through your plumbing drainage lines it almost always contains solid particles. These particles can be tiny pieces of dirt, grit, fabric fibers, hair, whiskers, food particles, etc. Some of these can break down naturally and others may never break down.
Septic Tank Video
Watch this video to see a septic tank and special leach field that goes under a roadway!
It is the job of the tank to make sure that these particles no matter how large or how small do not make it into the drain field.
Remember my friend? His company's septic tank was filled to the brim with cast iron shavings from their manufacturing process. Your septic tank might fill up with plastic army men, sand, or dirt if you have my son visit for a while. Get the picture?
Septic Drainfield or Leach Field
The drainfield is a system of perforated pipes that lie near the surface in sand or gravel filled trenches. If you have special site conditions, your drain field may consist of mounds or long interconnected trenches setup for hillsides. In any event, an equal amount of partially treated wastewater from the tank enters the drain field every time you send a slug of water from your house towards the tank.
The drain field must not accept solid particles. If it does, the perforations in the pipes, the sand, gravel, and eventually the soil will clog up. When this happens, the septic system dies. It can no longer function.
If your system is working properly, the partially treated wastewater from the tank slowly enters the ground. Once in the soil, tiny microorganisms and oxygen work to attack any waste particles, bacteria, viruses, etc. that are in the polluted water. As long as the soil is not waterlogged, the soil will purify the wastewater.
Septic systems are a great example of a simple system that works. As long as you understand how they work and keep the tanks free of debris, you will be in good shape. Don't underestimate their ability to safely treat wastewater
Oxygen Works Best
Municipal sewer plants break down sewage using air. They aerate the waste in any number of ways before dumping it in the nearby river or ocean.
You can get pumps with propellers that inject air into your septic tank. Think of this as a giant blender.
You can also just add powdered oxygen bleach to your septic system.
Oxygen bleach has been around for some time but only in the past 10 years has it started to be widely available to consumers like you and me. Previously, it was only used by large commercial and institutional organizations. Ads for oxygen bleach can be seen on cable TV infomercials. You may have noticed it in hardware stores or home centers where it is sold as a deck cleaner. One brand is Wolman's Deck Brightener. The problem with many of these products is they may contain up to 30% fillers that can harm septic systems.
Sizing Requirements for Septic Tanks
Septic tanks must be sized properly. If they are too small bad things will happen to your drain field. Wastewater will flow too quickly into your drain field. If this happens there is a good chance that suspended solid particles will not have had enough time to settle to the bottom of the tank. These particles will eventually clog the drain field.
Proper design of tanks and sizing will permit a two day holding period for wastewater. This is usually enough time for the solid particles to sink to the bottom of the tank.
Septic tank size is a direct function of the number of occupants in a home. This number is generally associated with the number of bedrooms in a house. However, this rule is not always accurate! A 3 bedroom house that has two adults and two kids will send much less water into the tank than a 3 bedroom house that has 2 adults and 6 kids(such households exist)! If you feel that you have or might have more occupants than average, you had better talk with your local board of health officials.
Accepted sizing recommendations usually spell out that you should multiply the number of bedrooms, or rooms used as bedrooms by 150 gallons. Then multiply this by 2. this will give you the minimum capacity for tank size.
Example:
4 bedrooms x 150 = 600 600 x 2 = 1,200 gallons
Standard tanks are usually available in 750; 1,000; 1,200; and 1,500 gallon capacities.
Septic System Do's & Don'ts
The long term health of your septic system is directly related to what you inject into it. If you abuse the system, you will have to have it pumped more frequently or worse yet, it may fail entirely (Remember, my friend!) If you follow some of these do's and don'ts, you should get many, many years of trouble free service from your septic system.
Do's
Determine the location of your septic tank and drain field. It is almost always down slope from your house. Look to see where the main plumbing drain leaves your house.
Have your tank inspected by a qualified service company annually. These inspections will tell you when the tank must be pumped clean of accumulated solid material. Keep the inspection portals and manhole covers at ground level.
If installing a new system, make an accurate map of the tank location and the shape, trench location, and extent of the drain field. Plan for future house expansion. In other words, do not put the tank or the drain field too close to the house. A future room addition may require you to move the tank!
Fix leaky faucets or toilets quickly. Excess water flowing into the system will send solid particles into the drain field! Excess water will flood the soil in the drain field!
Divert water from parking areas, downspouts, sumps, footing drains, etc. away from the drain field. Drain fields must be as dry as possible in order for the soil to naturally cleanse the wastewater.
Don'ts
Avoid introducing any unnecessary solid particle into your plumbing system. This includes things like coffee grinds, nut shells, dental floss, kitty litter, female hygiene products of any kind, cigarette butts, sand, gravel, etc. All of these things will fill the tank prematurely!
Do not plant trees anywhere near the drain field. the roots of trees will naturally migrate to the perforated pipes. These roots will completely clog the pipes! Natural grass cover is the best.

Click here to view Tim's video on Septic Systems.
Do not park cars, drive over, or allow heavy trucks onto the drain field area. This will compact the soil and cut off the necessary oxygen required to help breakdown the wastewater.
Absolutely do not introduce paints (even latex!!!), solvents (gasoline, thinners, alcohol, etc.), varnishes, grease, cooking oil, pesticides, photographic chemicals, etc. into the septic system. These will kill the natural microbes that breakdown organic solid compounds in your tank!
Garbage disposers are fine but large food particles that pass through a sink strainer are bad. Disposers create a mush that the bacteria in septic tanks can handle. Large solid food particles can turn to sludge before they are broken down.
Avoid using septic tank additives. A healthy septic tank and drain field has everything it needs. The natural bacteria from our human waste gives the tank all the additives that are required. Extra oxygen is just about the only thing you can introduce that may help.
Don't pave over the drain field. Paving materials prevent natural evaporation of moisture. The grass cover mentioned above sucks water from the drain field.
Avoid trying to repair or modify your septic system by yourself. These systems must be designed and engineered by professionals.
!! ALERT ALERT ALERT ALERT !!
Never attempt to inspect a septic tank by yourself! Deadly gases are in the tank. You can pass out in a matter of moments. The person trying to rescue you will do the same. Only qualified septic service people should remove manhole covers. Don't lean over and stick your head in a tank!!!!!
|
Helpful Literature and Videos
The Small Flows Clearing House, located at West Virginia University, is command central for septic system information. They have an abundant supply of pamphlets, videos, and booklets that will help you design, construct, and maintain a septic system. They also publish a wonderful quarterly newsletter called Pipeline. I suggest you call them and ask them to send you as much free literature as possible. They will also send you an order form for their wonderful videos and books. You will not regret making this call! Tell them you heard it from me! 800-624-8301
Column B117