DEAR TIM: The instructions on the can of paint I am getting ready to use say to use a primer paint on bare wood. Is that really necessary? It seems like a waste of time. What are the benefits of using paint primer? I feel the paint company just wants another sale and they are trying to slow me down. I have never used primers before, and the paint I use seems to hold up. If you do convince me, is there a special primer I should use? Jane G., Sierra Vista, AZ
DEAR JACKIE: I am sure the things you painted before survived the lack of primer, but I am here to tell you that the finished product would have been much better had you used a primer. Paint primers are very necessary, and they serve several very important functions.
A paint primer is a special paint. It is formulated to do several mission-critical things, the least of which is create a superior bond to the object being painted. Keep in mind that for all intents and purposes, most paints are simply high-performance coatings that are really glues with color in them. In other words, when applied correctly to the right things, paint can stick or adhere to something for a very long time, just as any glue applied out of a bottle does.
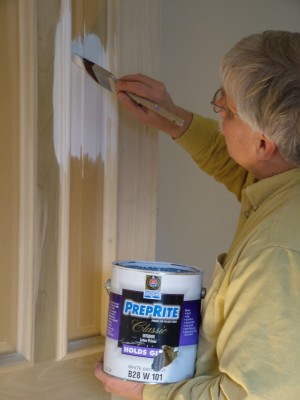
This bare wood door needs a coat of primer to make the finish paint glow. PHOTO CREDIT: Brent Walter
The chemists who work for paint companies formulate primers so they are very sticky. The grab onto surfaces like briars to your pants. What's more, the dried surface of many primers is formulated to physically and chemically bond to the finish paint, if you apply the finish paint within 24 hours of applying the primer.
Certain primer paints also serve two other functions - they seal a porous surface, and they even out the texture of the object so the finish paints think they are being applied over a sheet of glass.
If you were to look at the surface of the wood you are about to paint under a microscope, you would be shocked at how rough it really is, even after you have sanded it. What's more, depending upon the species of wood you are painting and its grain pattern, you can have widely varying levels of porosity between the light grained spring wood and the darker grain bands of summer wood.
If you were to paint over wood without a primer, you might be able to see these grain bands. The finish paint would look dull over the light-colored spring wood, but glossier over the darker bands of wood. This happens because the paints soaks into the light-colored spring wood. A primer-sealer paint seals the surface of wood so the finish paint does not soak into it. This allows you to have even gloss over the wood that is painted.
Many paint primers for wood have lots of dense pigments in them that act as microscopic liquid-spackling compound. The pigments fill in all of the low spots in the wood so the finish paint will look like satin.
Modern primers are often water-based and dry very rapidly. Some can be recoated with finish paint in less than an hour. Using a primer will actually speed up the job, not slow you down.
I urge you to always use a primer if the paint can label suggests it. In fact, pay attention to what the primer says to use, as the primers are often formulated to work with specific finish paints. I can assure you that you will achieve better-looking and longer-lasting results if you use a primer, no matter if you are painting bare wood, metal, plastic or just about any surface - even ceramic tile!
After painting bare wood with a water-based primer, the wood may seem rougher than before you started. This frequently happens for two reasons - the water in the paint can raise the grain of the bare wood, and you feel some of the coarse pigments in the paint. For truly professional results, you need to lightly sand the primer before you apply the first coat of finish paint. The primers sand very easily, so this task will not be a chore to do.
Try to recoat the primer with a finish coat of paint within 12 hours if at all possible. The sooner you cover the primer with finish paint, after you have passed the minimum recoat time period, the better the bond will be between the two paints.
Be sure to read the label instructions of the primer and follow those to the letter. If it says to apply the primer to a clean, dry surface, it means it. Clean means washing the surface with soap and water if necessary to remove dirt, oils, grease, tree sap, etc.
Column 706