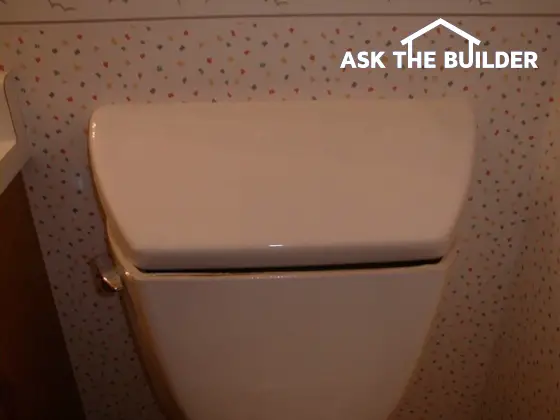
This silly toilet tank lid can be nearly impossible to find 20 years down the road. It may pay to have an extra one on hand for important toilets that your guests use. Or you may end up having to install a completely new toilet just to get a new lid!
Finding Replacement Parts
DEAR TIM: I have just spent two vacation days trying to locate replacement parts for fixtures around my home. Replacement ceramic tile and a simple toilet tank lid were nowhere to be found. I was able to get replacement parts for an older faucet, but I had to visit three stores to find them. Are there businesses that sell out of stock building materials? Surely there must be an alternative or a way to avoid wasting all of this time. Shelly A. Wilmington, OH
DEAR SHELLY: A similar thing happened to me not too long ago but my search for parts lasted about 2 minutes. I needed to replace a chipped piece of ceramic tile in one of my bathrooms. I went into my basement and found the exact piece I needed. Years of building has taught me to order extra materials and save scrap material when possible. You just never know when it might come in handy.
Replacement parts for many of the fixtures in your house are often readily available when the house is being built. But as time passes, some of these parts can become extinct. Colors and styles change as do peoples' tastes. My in-laws have a pink and gray ceramic tile bathroom. It was the rage 40 years ago when their house was built but finding replacement tile today would be next to impossible. It is unrealistic to expect tile stores to take up valuable stock space with tile that is no longer popular.
Some cities and towns do have shops that specialize in used and salvaged building materials. I am fortunate where I live. There are at least three businesses that have a wide variety of unusual old building supplies. One of them even stocks panes of glass that are over 100 years old. I know because I used to sell it to them when I would remove it from old houses that were getting new replacement windows. These stores are often listed in the Yellow Pages portion of the phone book. Look under the Building Materials, Salvaged Materials, or Architectural Antiques headings of the phone book.
If you are connected to the Internet you might also have some luck at the various auction or swap web sites. The power of the Internet allows a person to have a yard sale and the rest of the world can be the customer base. I happen to know a person right now who is remodeling his kitchen. He hates the old plastic ceramic tile on the walls and was going to throw it away. When I told him there was a market for it, he was surprised. There is an enormous amount of treasure out there, you just have to go hunting for it.
I feel the best way to prepare for the future is to buy replacement parts when you build or very soon after your house is built. Things as common as circuit breakers can become hard to find. If a manufacturer changes an electric panel design, you may be in a bind down the road when you want to add a circuit or two. The trick is to buy things that do not go bad. Ceramic tile, faucet parts, specialty glass for light fixtures, circuit breakers, electric switches, roof shingles, brick, etc. are examples of things that simply don't go bad if stored in a cool, dry location. I have many of these things stockpiled from when I built my own home and believe me, they have come in handy on more than one occasion.
Creating a stockpile like this may only cost several hundred dollars. Circuit breakers often cost less than $5 each. Ceramic tile may be only $3 per square foot. A box of vinyl tile may cost just $40. A square of shingles could cost just $30 now but the color you need may be unavailable in just five years. To make sure stockpiled items don't get thrown away, mark them clearly. Certain items like faucet parts can be placed in plastic zip lock bags and be attached to the inside of sink and lavatory cabinets. Each time you open the cabinet door you will get that warm and fuzzy feeling that you are prepared for that upcoming leak!
Column 329