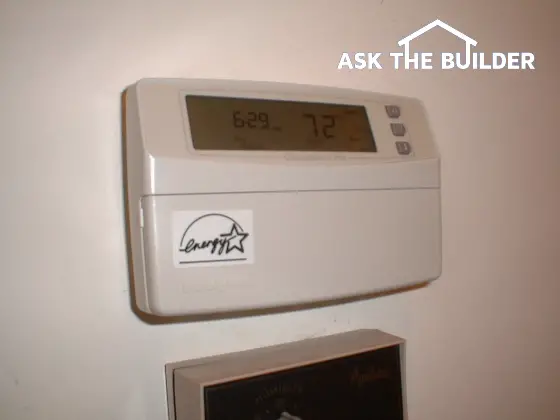
My programmable thermostat works very well. It is dependable and has four different time periods that will cycle on and off each day.
Programmable Thermostats
DEAR TIM: Electricity and heating fuel prices are soaring. I need to conserve energy. Will a programmable thermostat really help me save money? How can you maximize energy savings when using one? Robin T., Auburn, NY
DEAR ROBIN: You bet a programmable thermostat can save you energy dollars. The amount of savings depends upon many factors. Some people save more than others because they fine tune the thermostat for maximum performance. But keep in mind that these wonderful thermostats can't make a silk purse out of a sow's ear. In other words, if your furnace and air conditioning system is poorly designed and not sized properly to match the heating and cooling needs of your home, the thermostat may struggle to deliver the savings and comfort you desire.
Programmable thermostats are not new. They have been around for years in one form or another. But advancements in electronics and small computer chips have allowed these instruments to become more reliable and affordable. These devices allow you to adjust the temperature in your home up to four times a day. The thermostats have a memory and will raise and lower the temperature at different times so that when you wake up or come home the house is at the desired temperature. When programmed correctly they will also adjust the temperature in the home when you have left for the day or are sleeping.
The typical programmable thermostat has four setting periods: Wake, Leave, Return, Sleep. You simply enter these times into the thermostat and then set the desired temperatures for both the heating season and cooling season if you use air conditioning. To optimize energy savings, set the thermostat back eight to ten degrees when you are away and sleeping. These work best in the heating season. You probably will find that these setbacks are too much if you are using air conditioning. For the most part, air conditioners do not recover as quickly as furnaces.
It often requires a few days to properly adjust these thermostats. You need to learn how quickly your furnace or air conditioner can recover from the set back temperature. In my own home, I have found that it takes just 30 minutes for my furnace to make up the eight degree difference. But it takes 90 minutes for it to drop the temperature just four degrees when cooling. Once you learn how long it takes to go up and down, you can program the furnace or air conditioner to turn on at the right time so that when you wake up and/or come home, the house is at the perfect temperature.
You also need to learn how long it takes to go the other direction. There is no reason why the furnace or air conditioner should be still running just before you leave the house or go to bed. The thermostat should set the temperature back some time before so that you are out the door or under the covers just before it gets uncomfortable.
Not all programmable thermostats are created equal. I suggest you buy a high quality one. Some poor quality thermostats contain electrical components that create false heat. This can cause up to an eight degree temperature difference between the actual air temperature and what the thermostat reads. The best thermostats carry an Energy Star label and cost more money because they contain high quality components.
If you have an existing programmable thermostat, look to see if it contains batteries. If so, change these batteries annually. Be sure the thermostat has indeed been programmed. Often a programmable thermostat is operating as a normal one and the interior temperature never changes. Check the thermostat periodically to see if indeed it is raising and lowering the temperature. Come home early one day to see what is going on ... or off!
Related Column: Programmable Thermostat Sources
Column 367