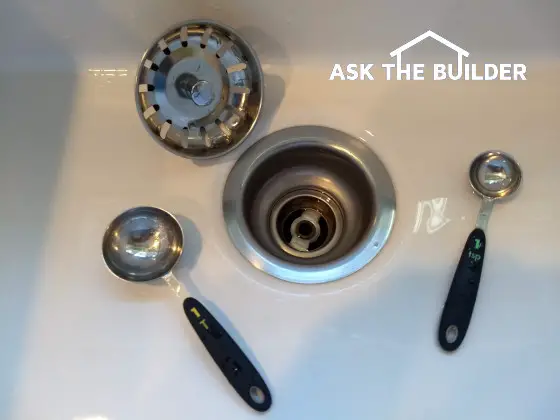
This is a typical kitchen sink strainer and strainer basket. Note the slots and holes in both. (C) Copyright 2019 Tim Carter
Clog-Free Kitchen and Bath Drains
Yesterday, I was perusing a national news website whose headlines more and more are reminding me of the traditional sensational tabloids that might have a story about a lawn being stolen. Being a syndicated newspaper columnist, I find this transition most interesting.
One particular headline caught my eye as it talked about the five things you should NEVER put down your kitchen drain. I’ve been a master plumber since age 29 and have had the very good fortune to replace old kitchen drain lines and unclog newer ones choked with gunk and who-knows-what. I thought I might discover something I didn’t know.
While there were one or two good tips in the article a few of them had me scratching my head wondering if the author had ever cleaned out a residential drain line to a kitchen or bathroom sink. I decided to share with you my experiences with residential drain lines and let you apply your own common sense. Beware, as a few of the images I’m about to render might make you squirm just a bit.
I think it’s best to describe what the inside of drain pipes look like when new and after they’ve been in use for years or decades. New cast iron, copper, galvanized iron, and plastic drain lines all are quite smooth on the inside of the pipe. You want smooth bore pipe so nothing gets snagged.
Unfortunately, a characteristic of older galvanized iron pipe is that it starts to develop a rough inner surface that actually starts to get clogged from small debris that grows hard-water deposits on the inside of the pipe wall. I’ve cut out galvanized iron drain lines from kitchen and bath walls and the entire inside of the pipe is choked off with this hard calcified buildup.
Fortunately, galvanized pipe is rarely used now and it can be found in older homes built between 1900 and the late 1950s. Plastic plumbing drain lines swept the industry by storm in the 1960s and have become the go-to material for almost all residential plumbing drain installations.
I want to briefly discuss the size of pipes and what passes through them with little effort. The drain pipe beneath the toilet in your home is most likely a 3-inch-diameter pipe. Your body, on a regular basis, produces solid cylindrical waste that often might be 1 and 1/4-inches in diameter. You then add paper waste to the toilet bowl, flush it and magically all of this ends up in a septic tank or your city’s sewage treatment plant.
Now think about the lowly kitchen or bathroom sink drain pipe. Just behind the wall of the sink, there’s probably a horizontal 1.5-inch-diameter pipe. Plumbers call this a branch arm. That horizontal pipe in a kitchen should travel no more than 42 inches where it connects to a vertical pipe, a stack, that should be at least 2 inches in diameter. Bathroom sink drains almost always connect to another 1.5-inch-diameter vertical stack instead of a 2-inch one.
Imagine the size of solid material that can pass through the branch arms to the stacks with little effort if enough water is assisting in the process. In other words, a green pea should have no problems passing through a kitchen drain pipe.
Here are some best practices to keep your kitchen and bathroom sink drains clog-free for decades now that you understand how things pass through pipes.
Never allow grease to go down a drain. It solidifies and will clog drain pipes. I set aside used paper towels in my kitchen that are quite clean to sop up liquid grease from cooking pots and pans. These towels are then thrown in the garbage.
Never allow flour and egg mixtures into your kitchen sink drains. Dump as much of this as possible into the garbage. Don’t allow clumps of flour to enter the drain. Fill the kitchen sink with water halfway and wash and emulsify the flour coating on the pans and bowls. Pull the sink stopper and allow this fine slurry to rush down the drain into the main building drain. As crazy as it sounds, flush a nearby toilet to send the slurry on its way to the sewer plant or septic tank.
Keep the basket strainer in your kitchen sink strainer and allow it to capture larger food debris. Dump the debris in the garbage, don’t use your fingers to push it through the slots in the strainer sending it down the drain.
If you use a disposer in your kitchen, fill your sink with water about halfway before you turn on the disposer. Remove the disposer drain cover and turn on the disposer. The giant slug of water will carry the sludge into the main building drain under your home. All too often homeowners turn off the water at the sink too early allowing the kitchen drain pipe to have a liquid slurry laying in the pipes.
Once a month pour a gallon of boiling water down your kitchen and bathroom sink. This hot water can dissolve rogue grease that somehow makes it into the drain and it can dissolve some cosmetics that may be lurking in a bathroom drain.
If you notice a bathroom sink is starting to drain slower and slower, take a few minutes and remove the stopper. The lever that makes your drain stopper go up and down does a great job of capturing hair. It takes only minutes of your time to remove that lever and any debris that’s in the drain tailpiece where the lever operates. There are quite a few videos on YouTube showing you how to easily remove and reinstall this simple part of a bathroom sink.
Once a month pour a bucket of water into your sinks to get as much water as possible flowing down the drain as fast as possible. This is the closest thing you can do as a homeowner to pressure wash the inside of drain lines. Doing this can save you hundreds of dollars that you’d otherwise have to pay a drain-cleaning service should you abuse your drain lines.
Column 1284