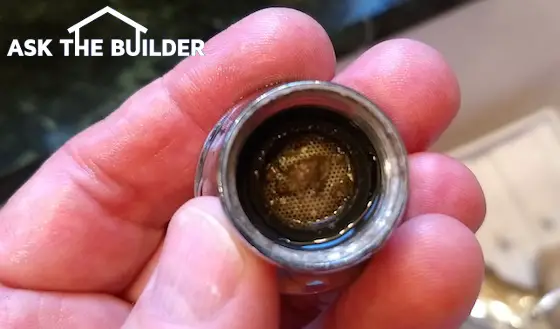
Low water pressure in faucets is almost always caused by debris and sediment in the aerator at the tip of the faucet. This gunk can be unhealthy too! Copyright 2018 Tim Carter
Low water pressure in faucets is caused by debris and sediment in either the aerator or the valve cartridge. Remove the aerator first and inspect it for sediment, goo, or hard-water deposits.
Revised February 2018 and mentioned in the February 13, 2018 Newsletter and April 29, 2010 Newsletter.
Low Water Pressure in Faucet TIPS
- Remove aerator from tip of vanity or kitchen sink faucet
- Check screen for sediment and pieces of sand
- Soak in hot white vinegar to remove hard water deposits
- Replace valve cartridge if problem persists
- CLICK HERE to get FREE BIDS from local plumbers
DEAR TIM: Several weeks ago our whirlpool faucet water pressure and volume dropped to half while I was filling the whirlpool with water. The pressure and volume slowly returned to normal.
At the same time, our kitchen faucet pressure and volume dropped even more than 50 percent. It has not returned to normal and gets worse each day. All other faucets seem to work fine and the toilets fill quickly. What happened? What is wrong and is it expensive to correct? Patty J., Sterling, VA
Related Links
Low Pressure in Shower Heads - Easy to Solve
How To Solve Low Pressure Problems Without a Plumber
Free & Fast Bids
CLICK HERE to get FREE & FAST BIDS from local plumbers who can fix pressure problems in your home or condo.
DEAR PATTY: I've been a master plumber for decades and I'm sure I can help solve your problem. Strange residential water pressure problems are far more common today than they were years ago.
Part of the dilemma has to do with the internal design of many modern faucet valves and another part of the problem is directly related to natural resource conservation measures.
Low Water Pressure Caused By Small Clogged Pathways
Years ago many standard kitchen, bath, and shower faucets had rubber and plastic washers that contacted a circular valve seat inside the faucet. As you opened a faucet the washer would pull away from the valve seat creating a very large pathway for water to flow through.
In many faucets the pathway was so big, a small, round BB could easily pass through the faucet and into the sink or a glass of water. This older design allowed vast amounts of water to flow through a faucet and this is not a great thing when we have a growing population and limited fresh-water supplies.
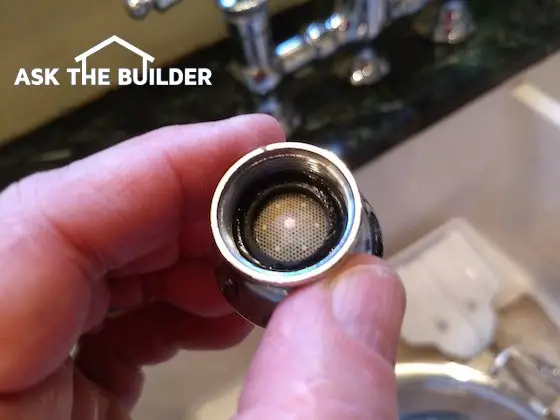
This is the same aerator as in the top photo. I cleaned it in just minutes with a small brush and a toothpick. Copyright 2018 Tim Carter
What Part Inside a Faucets is to Blame For Low Pressure?
But many of today's modern faucets have washerless cartridges inside the body of the faucet. The modern cartridge replaces the older washer and valve seat design which controls water flow. The pathway through which water passes in these cartridges is much smaller than old faucets. These small passageways can get clogged with small pieces of sand or sediment.
Many of today's faucets also have an aerator at the end of the faucet. These devices are often made up of several small parts including a flow restrictor and a screen with very small holes. These also can get clogged very fast with very tiny pieces of sand or sediment.
If you take the aerator apart, you will discover extremely small holes in round disks made of plastic or metal. The water flowing from the faucet must pass through these tiny orifices.
Sediment & Hard-Water Deposits The Culprits
I'm convinced the drop in water volume and pressure at the two faucets was caused by small pieces of sediment or some other debris that clogged a passageway within the valve cartridge and/or the tiny orifices within the aerator and or a flow restrictor. This is an extremely common problem for many homeowners.
CLICK HERE to get FREE & FAST BIDS from local plumbers to solve your faucet problem.
The sediment can form within a faucet or its parts depending upon the hardness of your water. Sediment also forms as a scale on the inside of municipal water supply pipes and the water lines inside your home.
Pieces of this sediment can break off and be transported through the water lines as water moves towards a faucet. Small pieces of sand or rocks can enter a water system, especially those of people who use a private well. These can block the pathways within your faucets.
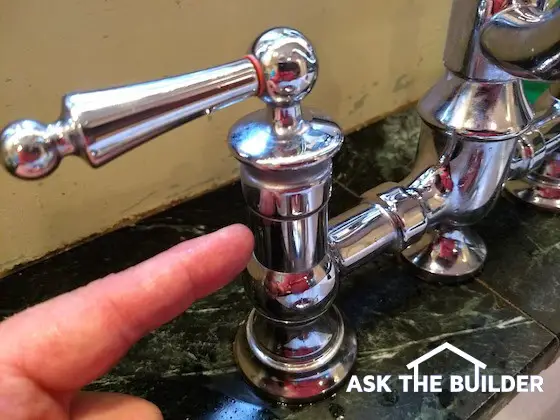
Low water pressure could be caused by a clogged cartridge. You'll find the cartridge just under this decorative faucet handle cover. Copyright 2018 Tim Carter
These low water pressure and flow problems are very common just after a water main break in a municipal water system. Sand, dirt and other debris can enter municipal piping systems when a water main fractures. Once the water main is repaired, this debris is transported through the water system and can end up in your home.
What Can Clog Water Lines or Aerators?
Small shavings of piping, soldering flux, sediment, etc. can also be carried through your own pipes when repairs are made to your plumbing system or new piping is added to your home. Problems can also happen by simply turning on or off a main or secondary water control valve within your home by a plumber who might be installing a new faucet or performing a repair.
It's important to realize when you install a new faucet, like this American Standard Saybrook one, that you remove the aerator before you turn on the water. Turning off shut-off valves and moving supply tubes around can loosen debris that will clog the new aerator.
Can a Water Main Break Clog Aerators?
If a city water main or water line inside your home is drained and then refilled with water, the incoming water can break off tremendous amounts of sediment and carry it through the water system. This happens when the surge of water rushes into the empty pipes creating a miniature tsunami of roiling water and sediment as the water fills the pipes.
CLICK HERE to get FREE & FAST BIDS from local plumbers who can fix pressure problems in your home or condo.
Is it Expensive to Fix a Faucet Aerator?
It is not expensive to correct the problem. The first thing I would look at are the aerators in any faucet that is giving you problems. Carefully remove the aerator and pay attention to how the different parts are assembled.
Look at the parts, including the screening at the tip of the aerator, to ensure all parts are free of debris and all pathways are clear. Use tiny straight pins to open up any closed holes in these parts. You may have to soak the parts in warm, white vinegar overnight to removed caked, hard-water deposits that can build up within the aerator.
If, after reassembling the aerator, the water pressure and volume are still low, this means the problem is probably in the valve cartridge. The owner's manual that came with the faucet will show you how to remove and replace this common and inexpensive part. If you do not have the manual, try visiting the manufacturer's website for a technical bulletin showing you an exploded view of the faucet and its parts.
How Do You Flush Water Lines After A Repair?
To stop sediment from ending up inside the faucets in your home, it is best to open up an outside hose faucet or two to allow water to flow through them after you have completed a plumbing repair on your own home. These faucets often have the old-fashioned rubber or plastic washers. It is also a splendid idea to remove all faucet aerators before water is turned back on after a repair.
I suggest turning on the main water valve very slowly after a home plumbing repair. Be sure to have the outdoor faucets open before you do this. This allows the pressure within the piping system to build slowly and a majority of sediment might be carried outdoors if the repair was made between the location of the hose faucet and the main water inlet to the home.
If a water main breaks near your home and you notice there is no water in your home, do the same thing. While the water is off, go turn on one or two outside hose faucets. Also remove all faucet aerators. Since the water works employees will often turn the water on without notifying each homeowner, you may not get a warning. You want any sediment to be carried to these outside hose faucets or bypass faucet aerators if at all possible.
CLICK HERE to get FREE & FAST BIDS from local plumbers who can fix pressure problems in your home or condo.
Column 612