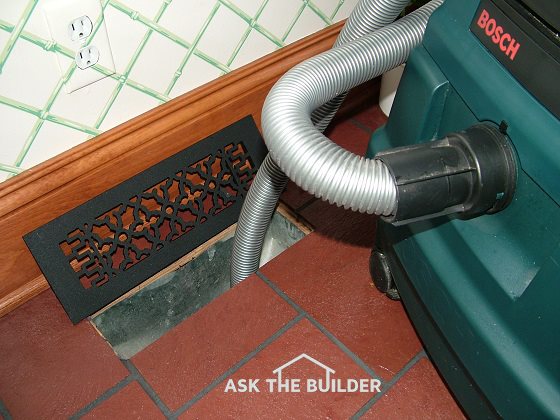
Use a wet-dry vacuum to suck out water from the ducts under a concrete slab. © 2017 Tim Carter
Water in Heating Ducts TIPS
- Water is in all soils
- Install a linear french drain to stop water
- WATCH linear french drain video below
- Consider relocating ducts to attic
- CLICK HERE to Get Tim's FREE & FUNNY Newsletter!
DEAR TIM: My husband and I live in a one-story home built on a slab. The home was built thirty years ago and we are the fourth owners. A few days ago I heard a bubbling noise coming from one of the floor heating vents.
I looked inside the vent and there was standing water! We pumped out water for two hours but the vents filled back up.
Where is the water coming from? How can we stop it? Do you think this problem was known by the previous owner and if so, do we have any recourse? Lynn F., Norcross, GA
DEAR LYNN: Oh my goodness. You've got a serious problem or two.
Water Is In Soil
Water is in just about every soil to one degree or another. I majored in geology in college and took a deep interest in hydrogeology - the study of groundwater.
This sub-surface water can not only cause enormous problems for people who own slabs, but those who have houses on crawlspaces and those built with full basements. Many people who own a slab house think they are immune to problems caused by subsurface water. But I can't begin to tell you how many emails I receive from people who have your identical problem: flooded buried heating and cooling ducts.
Water Moves Sideways
The problem is happening because water often moves sideways through soil instead of straight down. If you lived in parts of Florida or other parts of the USA where the soil is extremely sandy and drains like water passing through a cooking colander, we'd not be having this conversation. But my guess is that your home is built on soil that has a certain percentage of clay.
When rainwater falls onto the ground it readily passes through the topsoil as this upper level of the soil frequently contains lots of air voids. But as you go deeper into clay soils, the soil becomes extremely dense and often water is blocked from going down.
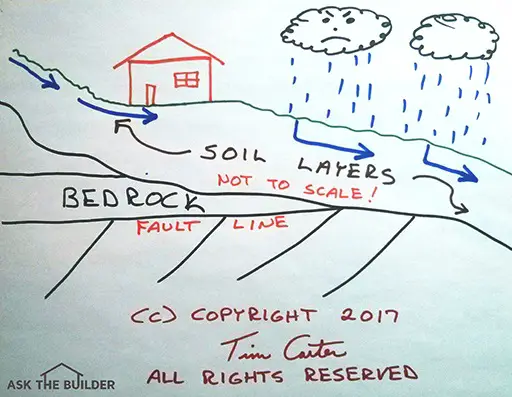
Here's a side view of a typical house. The black clouds release rain. It falls into the soil and starts to go down, but then sideways. The bedrock under the soil generally, but not always, follows the shape of the soil above it. Soil depths can vary from several feet to tens-of-feet thick. ©2017 Tim Carter
The water then starts to move sideways through the soil always flowing downhill and often pops to the surface as a spring. This water is the fuel that creates creeks, streams and rivers.
Thousands of Gallons
If you look outside your home and imagine the vast amount of soil that might be higher in elevation than your house, you might be amazed to learn that there are hundreds of thousands of gallons of water in the soil much of which is moving directly towards your home.
This water can easily find its way under the slab and into the ductwork beneath the slab. It's no wonder the vents filled back up after you pumped them out.
Capture The Water
Anyone who suffers from subsurface water that is invading any part of a house can stop it in almost all cases by capturing the water outdoors and then redirecting this water to the lowest part of the lot.
I've stopped water getting into ducts for decades with my Linear French Drain. CLICK HERE to get a fantastic Streaming Video showing you a DIY install method.
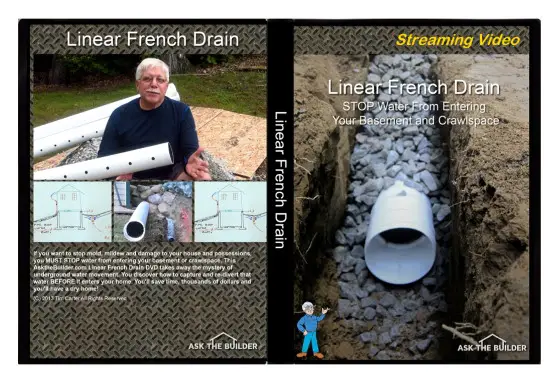
Do your own DIY install of a Linear French Drain with Tim Carter's time-tested methods and materials! CLICK IMAGE TO ORDER NOW!
Linear French Drain Video
Watch this quick video to show you how well the linear french drain in my Streaming Video works! Yes, it's the same drain the spring after it was installed!
Gutter In The Ground
Think of how gutters work on the roof of a house. Gutters capture the vast amount of water on a roof, channel it to various outlet holes within the gutter and then this water is piped away from the roof.
Ideally rainwater from a roof should be piped far away from a house and not be allowed to drop out of downspouts onto simple splash blocks adjacent to a foundation.
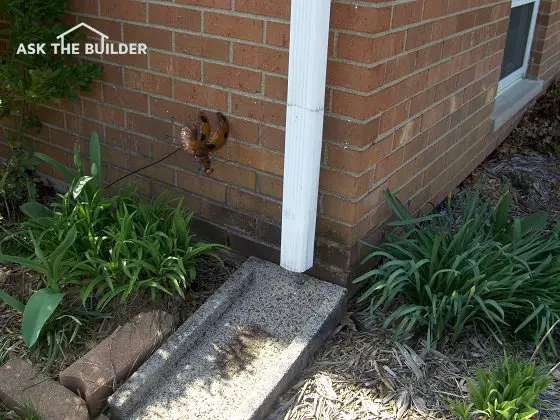
Splash blocks don't do much to channel water away from the foundation. © 2017 Roger Henthorn
Easy DIY Trench
You can capture the subsurface water by digging a trench around the outside of your home. This trench should be placed about 6 to 8-feet away from the edge of your home.
Call 811 first to have any underground utilities marked.
Dig this trench 6 inches wide and between 18 to 24 inches deep. The bottom of the trench should be parallel with the soil as it goes around your home. The trench should be extended away from the house and needs to end up at or near the lowest point of elevation on your building lot.
Level Trench
As the trench starts away from the house, make the bottom of the trench nearly level. As the ground falls away from the house, the trench will become shallower and eventually the bottom of the trench will be level with the top of the soil.
Best Gravel
You place a 1 or 2-inch layer of washed 1-inch diameter gravel in the bottom of the trench and then place a 4-inch diameter perforated pipe in the trench.
Fill the trench with more 1-inch washed gravel until you are within 1 or 2 inches of the top of the trench. You can place pieces of sod over the gravel.
Path Of Resistance
The subsurface water will now pass through the soil and enter the trench. Because it is easier to pass through gravel instead of soil, the water will drop down to the pipe.
There it will enter the pipe and be transported rapidly away from your home to the lowest part of your lot. The underside of your slab will never be saturated with water again.
Disclosure Law Weenie
If your state has a property disclosure law and the previous owners knew of this serious defect, they may have been obligated to bring this flaw to your attention. You should call the Realtor you used in the transaction to see if there was a property disclosure form that was not given to you.
The last house I purchased was sold to me by a liar. He lied about three or four water issues. My father-in-law had a saying about people like this: The mills of the gods grind slowly but thoroughly.
Fire Department Run Records
You can also stop by your local fire department. Just about every fire department in the nation keeps very good records of each time they leave the station and are asked to put out a fire or help in a situation.
If they were ever called to the house to help pump out the vents, you know the previous owner knew there was a problem. Well there is always the possibility your local fire department has mystic extra-sensory-perception powers!
Serious Health Issues
Water in buried heating and cooling ducts can cause serious health problems. The water in the ducts can initiate the growth of mold. Each time the heating or cooling system operates, the air moving through the ducts can blast millions of mold spores throughout the house.
Relocate Ducts
Although expensive to do, it might be a good idea to investigate the feasibility of moving the ducts into the attic space. The one-time expense may be a great way to protect the health of you and your family.
Believe it or not, it may be cheaper to abandon the under-floor ducts and put everything up in the attic. You'll save the cost of the linear french drain and cleaning the ducts out.
What's more, if you hire a real pro who knows how to properly size ducts so you have the proper flow into each room and the system maintains static pressure throughout, you could be more comfortable with the new ducts!
Column 561