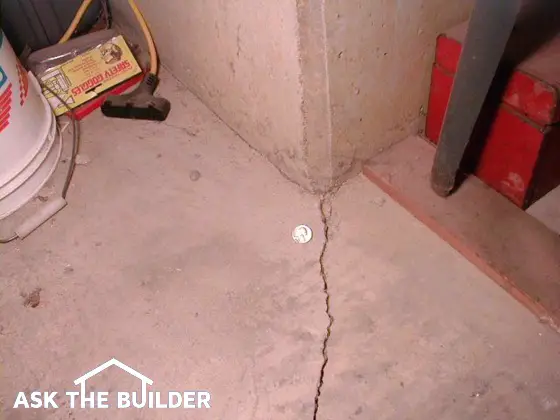
Settlement Cracks or Not? | This nasty wide crack in a basement concrete slab is not a settlement crack. It's a shrinkage crack.
Settlement Cracks - Very Rarely is it Settlement
I can't tell you how many thousands of times I have heard a new homeowner complain about settlement cracks. They seem to think the cracks that often develop early in the life of a new home occur because the entire house is sinking into the ground.
In certain cases, this absolutely can happen. Several years ago, I testified as an expert witness in a legal proceeding where a house had been built over uncompacted fill dirt that was placed over trees and other organic debris. The cracks that were tearing the house into several parts were indeed settlement cracks.
What is a shrinkage crack?
But 99 times out of 100, the cracks that you might see in a foundation wall, a concrete slab or in floors, walls, ceilings, ceramic tile grout, etc. are shrinkage cracks. Water is an ingredient of many building materials. It can be a natural ingredient as in the case of wood, or it can be added in the manufacturing process much like milk is added to a powder when making pancake batter. When this water evaporates from the material, the loss in volume can create a tension or tearing force within the building material.
CLICK or TAP HERE to get FREE BIDS from local handymen that can patch concrete shrinkage cracks.
How do you prevent settlement cracks?
To prevent real settlement cracks in your new home, you need to be somewhat proactive. In almost all areas of the nation, building inspectors are responsible for doing a visual inspection of the soil just before the foundation footer is poured. A trained inspector can often see or smell soil that may not be strong enough to support the weight of the new home.
But in the case I testified in, the fill soil brought into the building site looked fine. It appeared to be compacted sufficiently. But underneath the thin layer of good-looking soil trouble was lurking. Building inspectors are not expected to do extensive laboratory soil testing. They, as well as you, can request it if the soil seems suspect.
How Do You Repair Concrete Cracks?
CLICK or TAP HERE to discover the best product to use to repair concrete cracks. I use it all the time.
What can a topographic map tell me?
Before you buy a lot, ask to see the before and after topographic maps of the subdivision. If you study these maps you can see if the lot you are thinking of buying is one that contains fill dirt or one where dirt was removed to fill in an adjacent lot or two. Buying a lot that contains no fill dirt is the first step to prevent settlement cracks. It is no guarantee, but at least you remove poorly compacted fill dirt from the equation.
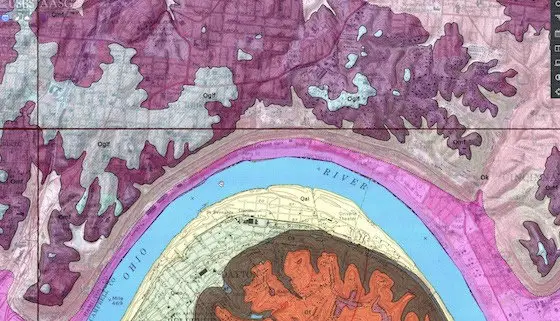
This is a topographic map and a geology map all in one. You can also get soil maps. Watch that video just below. Each color on the map represents a different rock formation.
Your local county agricultural agent may also have a free soil map for the asking. These invaluable tools often classify countless soil characteristics. One of them happens to be average strength. The soil map legend will help you identify weak soils and ones that are well suited to build upon. You do not have to have a degree in geology to understand these maps. They are frequently very user-friendly.
What is a foundation footing?
Once you are sure you are building upon a satisfactory soil, you need to make sure the footing and foundation will not budge under the weight of the home. The footing is perhaps the most fundamental aspect of a home foundation. It's a structural element not much different than a beam or a column. The footing is that part of a house or building that contacts the ground. Everything is built up from a footing.
What Does a Footing Do?
A footing's job is disperse the weight of the entire structure over a wide area. It's no different than the hard rubber pads you place under sofa or piano legs to minimize the imprint they might otherwise make on a hardwood or carpeted floor. If you simply poured a narrow foundation wall on most soils without the support of a footing, the foundation wall would sink into the soil like a jungle explorer in quicksand.
Is Footing Design Critical?
Footing design is critical. Local building codes may state a minimum width and thickness, but more is obviously better. A ten-inch-thick footer that is 24 or 28 inches wide is superb in most cases.
Should Reinforcing Steel Be in Footings?
The footing must contain a minimum of two continuous steel rods that are surrounded by the wet concrete.
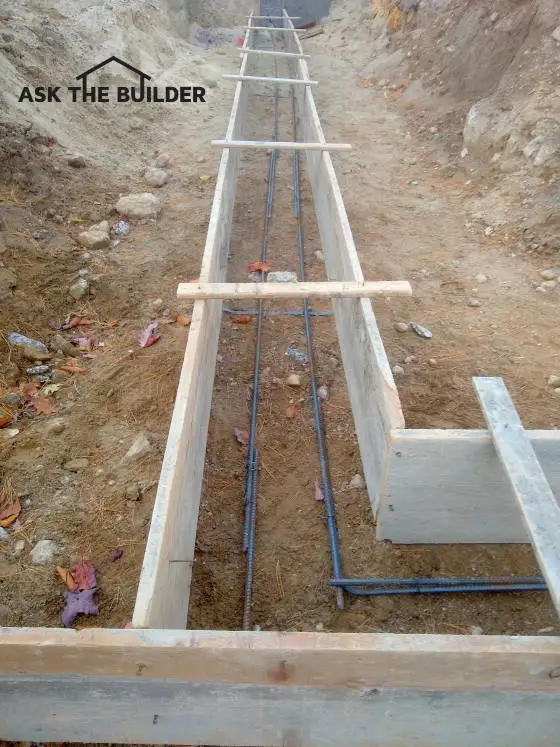
This is typical reinforcing steel in a footing. It will be raised up before the concrete truck arrives.
I prefer to use bars that are at least 5/8 inch in diameter, although 1/2-inch rods suffice. The steel should be placed in the lower third of the footing. If the footing is 10-inches thick, then be sure there are 3 inches of concrete UNDER the steel rods.
Keep in mind that the concrete used to pour the footing is available in different strengths. It costs just a little bit more money to add strength. Specify 3,000 pounds per square inch(psi) at a bare minimum. If you can afford 3,500 psi concrete for the footing, order or specify it.
How thick should the foundation walls be?
Poured or cast-concrete foundation walls should be at least 8-inches thick and some taller longer walls should be no less than 10-inches thick.
Your foundation walls act as giant beams when they are placed on the footer. If you are planning for a full basement, they also do double duty as retaining walls. To prevent cracks, be sure you use similar strength concrete as in the footers. The foundation walls must also get thicker as the walls get taller. Eight inch thick walls are fine where they may only have 5 or 6 feet of fill dirt up against them, but if you have more, I would specify a ten inch thick wall.
Is Steel Reinforcing Important in Foundation Walls?
Steel reinforcing is also important in foundation walls. Typically, a builder might place two rows of steel in the lower and upper portion of the wall. If you want bulletproof concrete walls that will stand the test of time, give serious consideration to extra horizontal steel as well as vertical steel bars that lock into the footer and continue up into the top of the foundation wall. Vertical steel bars help prevent horizontal cracks in the foundation walls.
Is it possible to help prevent foundation cracks once the house is built?
Yes. You can prevent foundation cracks by keeping the clay soil damp all year. You can install simple vertical watering holes to deep water the soil using a hand auger and filling the holes with rounded pea gravel.
Watch this video.
Column NH017