DEAR TIM: The floor to ceiling windows in my new house are beautiful, but I feel like a turkey in an oven when the sun streams through them. It seems as if my fabulous oriental rugs are fading before my eyes. Will the window film products keep me comfortable? Do they really stop fading in carpets, drapes and furniture? Are these products do-it-yourself friendly? Sally P., Chicago, IL
DEAR SALLY: Solar radiation that comes through unprotected glass can be intense. I know this from all of the years of installing new windows on sunny days. If you think you have it bad, travel to the sunny southwest or southeast USA where solar heat gain is a serious issue. The window film industry is highly advanced and there are any number of window film products that will work to control heat gain, heat loss, ultraviolet (UV) infiltration and common glare.
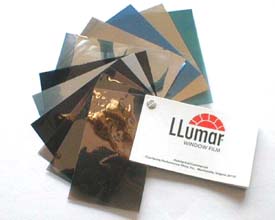
Here is a fan pack of the many different window films that are available. There are several manufacturers that make very high-quality films. Photo by: Tim Carter
The window film industry is one of those happened-by-accident stories. Back in the 1960's a person working for a greeting card company made several thin plastic films for a 25 year anniversary card series. He held the silver colored film up to a window to view it and noticed that it blocked significant amounts of heat energy. The window film industry was born!
Different metals are actually vaporized or sputtered onto thin polyester films. These metals work to reflect heat back to its source. Different amounts and types of metal can be applied to the films to achieve different heat blocking levels of performance. There are many different types of heat blocking window films. This allows you to choose one specific to your needs.
Special factory applied adhesives that do not distort visible light are used to attach these films to perfectly clean glass. The UV protection offered by the films is accidental. The films must be treated with a special chemical so that UV radiation doesn't breakdown and discolor the films. Old fashioned or low quality adhesive tape that yellows and becomes brittle is a good example of what UV rays will do to plastic films that don't have this special ingredient.
Colored window films can also be purchased. The color is actually imparted into the polyester film or adhesive with a dye. Some window films are one single layer while other specialized films can have up to 3 layers. The multi-layered products do a great job of protecting the ultra-thin metallic coatings.
The window films will slow down but not stop the fading process. Approximately 40 percent of fade problems can be attributed to UV radiation. The remainder is actually caused by visible light, heat, and components in the air. Your fabrics and carpets will continue to fade, but the window films do a swell job of retarding this process.
Window film installation is not a do-it-yourself project. Certain window films can not be applied to certain types and sizes of windows. Large expanses of glass can be subjected to extreme thermal stress if the wrong film is applied to a window that is too big. Some films should not be applied to clear glass thicker than 3/8 inch. Windows that are in concrete, solid aluminum or steel frames can sometimes cause problems. In other words, a professional needs to look at your windows and advise you as to what film can be safely installed on your glass.
Furthermore, the glass must be cleaned professionally for the films to be invisible once installed. Bubbles, wrinkles, and other imperfections can become a reality if an untrained person begins to install these special window films.
The window films can save you money in the long run. Most of them can be professionally installed for between $5 and $10 per square foot. Because the film colors are highly consistent, you might want to do a room or side of your house at different times if cost is an issue.
Companion Articles: Window Film, Window Films, Window Film FAQ, Window Film Companies
Column 267